About
The Project
Engineering Teams
D3 Balance
Detection Machine
Results
Deliverables
References
|
 |
Team CERN
Collaboration
with Romania
|
CERN, the European
Organization for Nuclear Research, is a large particle
physics laboratory headquartered in Genève,
Switzerland. The organization is home to many European
scientists conducting research under medical and
technological applications, as well as astronomy
research. Founded in 1954, CERN has existed for 52
years.
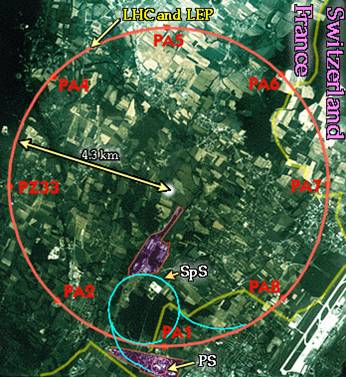
The world's
largest particle physics laboratory
CERN is in the process of
constructing the world’s largest particle collider, the
LHC (Large Hadron Collider). The facility will operate
on an array of superconductive magnets, interconnected
to form a circle. With over 2000 of these magnets,
quality control becomes a serious issue. All magnets
must be calibrated against reference magnets to ensure
operation is to specification.
CERN has developed a device
for this purpose. The apparatus is a rotating
measurement system, composed of several shaft segments
connected together. The segments contain coils that
rotate with the shaft; rotation is provided by a Twin
Rotating Unit or TRU. Upon rotation, the magnetic field
induces current in the coils; the output signals from
the coils give the magnetic flux, as a function of
angular position. This data is gathered for all dipole
and quadrupole magnets used in the LHC, and checked
against data collected from reference magnets. (Here
forth, this measurement device will be referred to as a
Rotating Coils Unit or RCU).
There exist two different
length RCU’s (one for dipoles and one for quadrupoles),
made up of different length shaft segments (1.2m and
0.75m, respectively). The segments use ceramic shafts
(Al2O3)
to support the coils and other components (see Figure
2‑1). These shafts are manufactured to tight geometric
tolerances, and further, the segments themselves are
manufactured with care.

Figure STYLEREF 1 \s 2‑ SEQ
Figure \* ARABIC \s 1 1 – Schematic of a shaft segment
showing main components: (a) ball bearing, (b) bronze
cage with roller, (c) Ti-bellow, (d) tangential coil,
(e) central coil, (f) dowel pin, (g) ceramic support,
(h) SiN Flange, (i) cable connector, (j) anticryostat,
(k) cold bore.
Currently, RCU’s rotate 3 times in
each opposite direction before reaching a constant speed
(1 Hz maximum) for data acquisition, a process that
takes about 15 seconds. However, faster measurement
times are desired. The revised method of operation
calls for continuous rotation of the RCU at 2 to 3 Hz
(10 Hz maximum), resulting in a measurement time of less
than 1 second. Still, problems may arise from this new
operation method: mechanical vibrations during rotation
may cause measurement errors. At present, a maximum
rotation rate of 1 Hz is used in order to avoid such
problems, however, since the segments have never been
balanced before (just carefully manufactured), they may
be inevitable at higher speeds.
|