Project
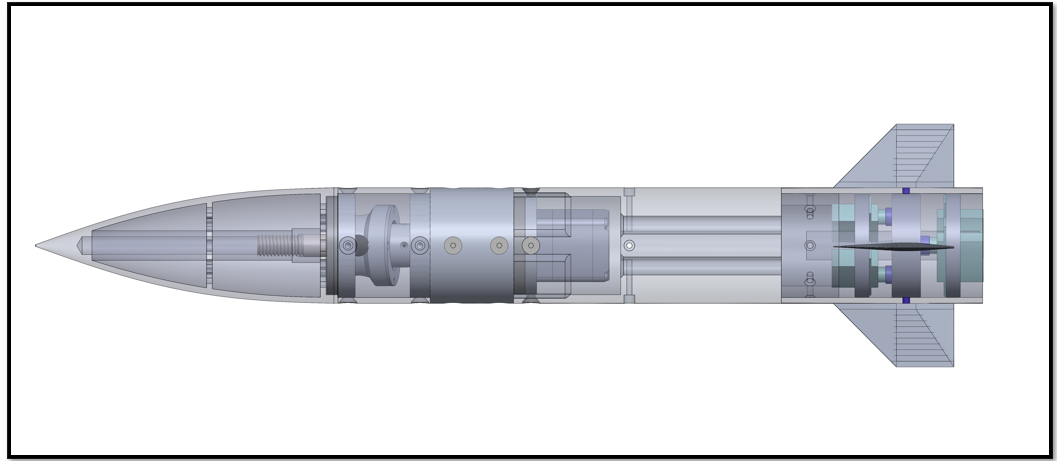
Smart Projectile Assembly
The objective of the project is to create a scale model of a projectile with an articulating nose cone and deflectable fins for subsonic wind tunnel testing.
While projectile technology has advanced significantly since the second World War, the U.S. military still seeks ways to improve the projectile’s accuracy. One approach that is of particular interest is the use of an actuating nose cone. This means the nose cone can move from its fixed position. Doing this allows the missile to change direction which improves its accuracy. To explore this, the Florida Center for Advanced Aero-Propulsion (FCAAP) has tasked the team with creating a model of a projectile with such a nose cone. Most large projectiles today have actuating fins, but no operational projectiles have an actuating nose cone. Therefore, this method needs to be researched. Our model still includes actuating fins to study the aerodynamic effect of the actuating nose cone on fin control. Ideally, combining an actuating nose cone with actuating fins will allow a greater improvement in flight accuracy when compared to the more basic alternatives. The fins are designed to attach to the model with up to 30 degrees of actuation for each fin. The nose cone is designed with up to 5 degrees of actuation. Because the real-world projectile will travel at such high speeds, this actuation must happen quickly. If it does not, there will be unwanted changes in the missile’s trajectory. Therefore, both the nose and fins are designed to actuate in less than 0.5 seconds. The model will be tested in a low-speed wind tunnel at FCAAP to understand the effects of the nose cone and fins. To control both components, stepper and Servo motors located inside the body of the model will be wired to a control device outside the tunnel. The nose cone and fins will move to various positions during testing, and data will be gathered to determine their effect on lift, drag, moment, and pressure coefficients.
Nose deflection between 0 to 5 degrees with resolution ±0.1
Static or dynamic deflectable fins
Time constant optimized to less than 0.5 seconds
Team
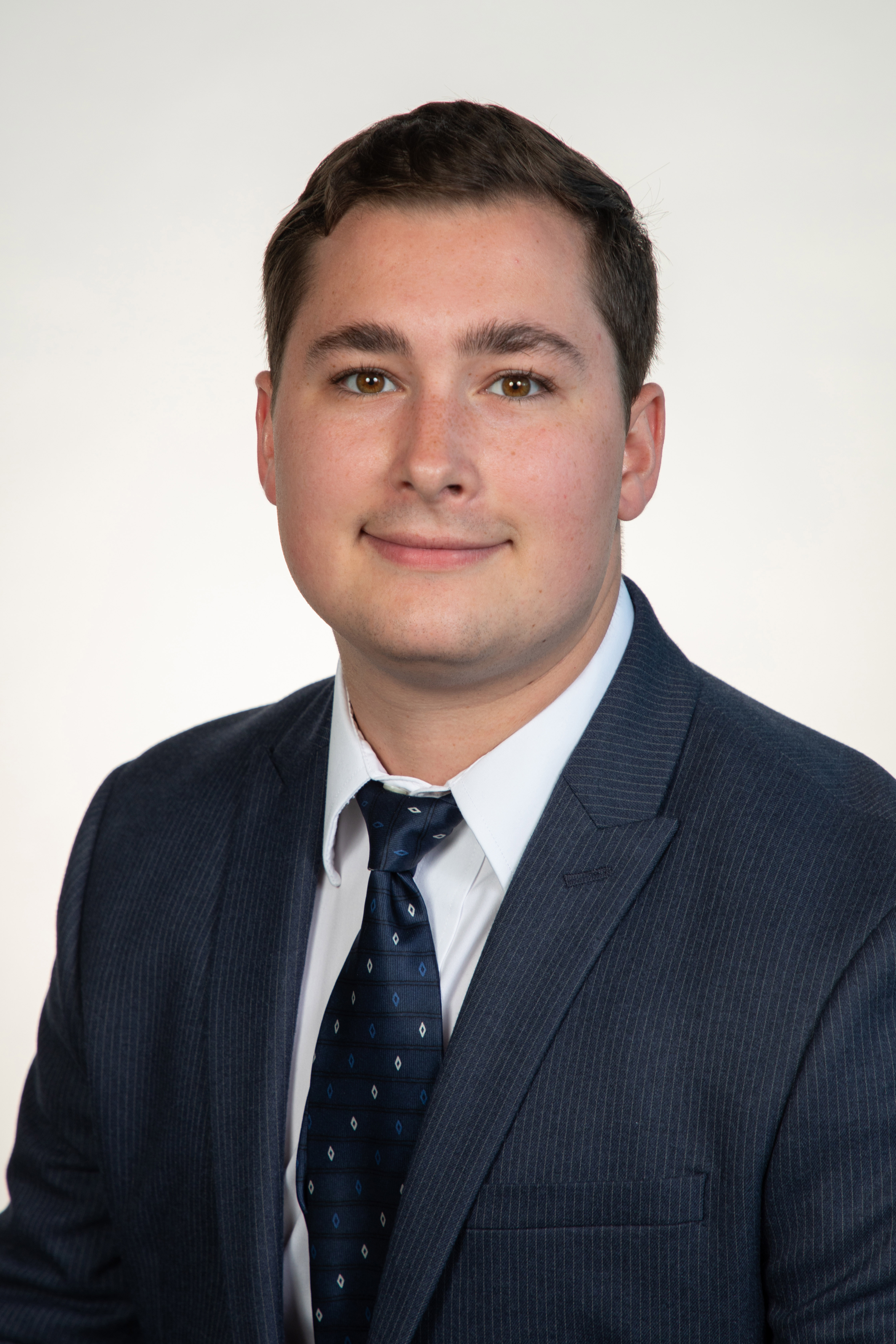
Jack Corbin
Fin Engineer
Jack Corbin is a senior in Mechanical Engineering looking to pursue a career in control systems. Jack assisted as the systems engineer.
jc19a@fsu.edu
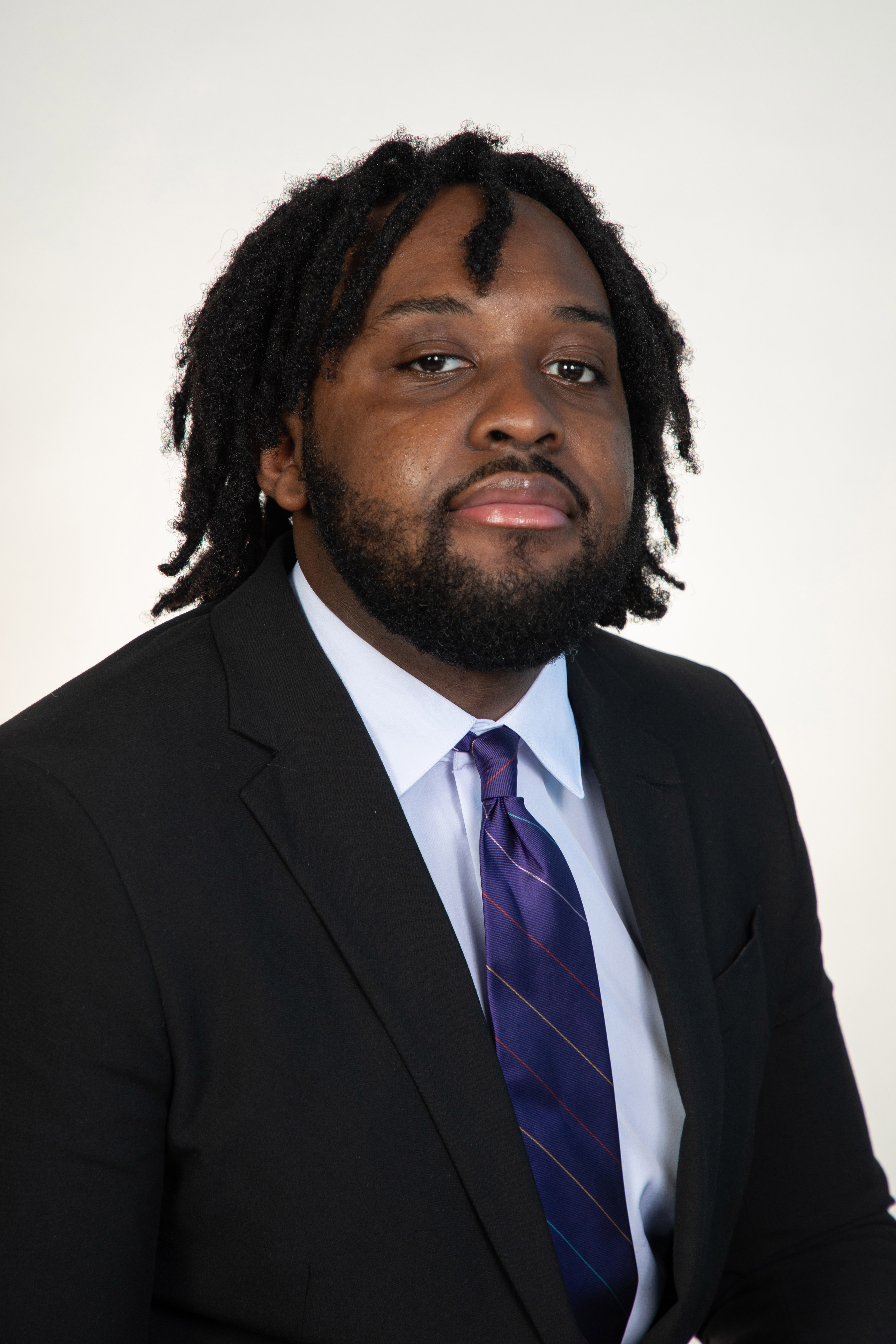
Prosley Dorcely
Research Engineer
Prosley is a mechanical engineering student graduating in spring 2023. Prosley hopes to join the workforce in the aviation, aerospace, or defense industries to gain knowledge on flight mechanics and aircraft systems.
pd18@fsu.edu
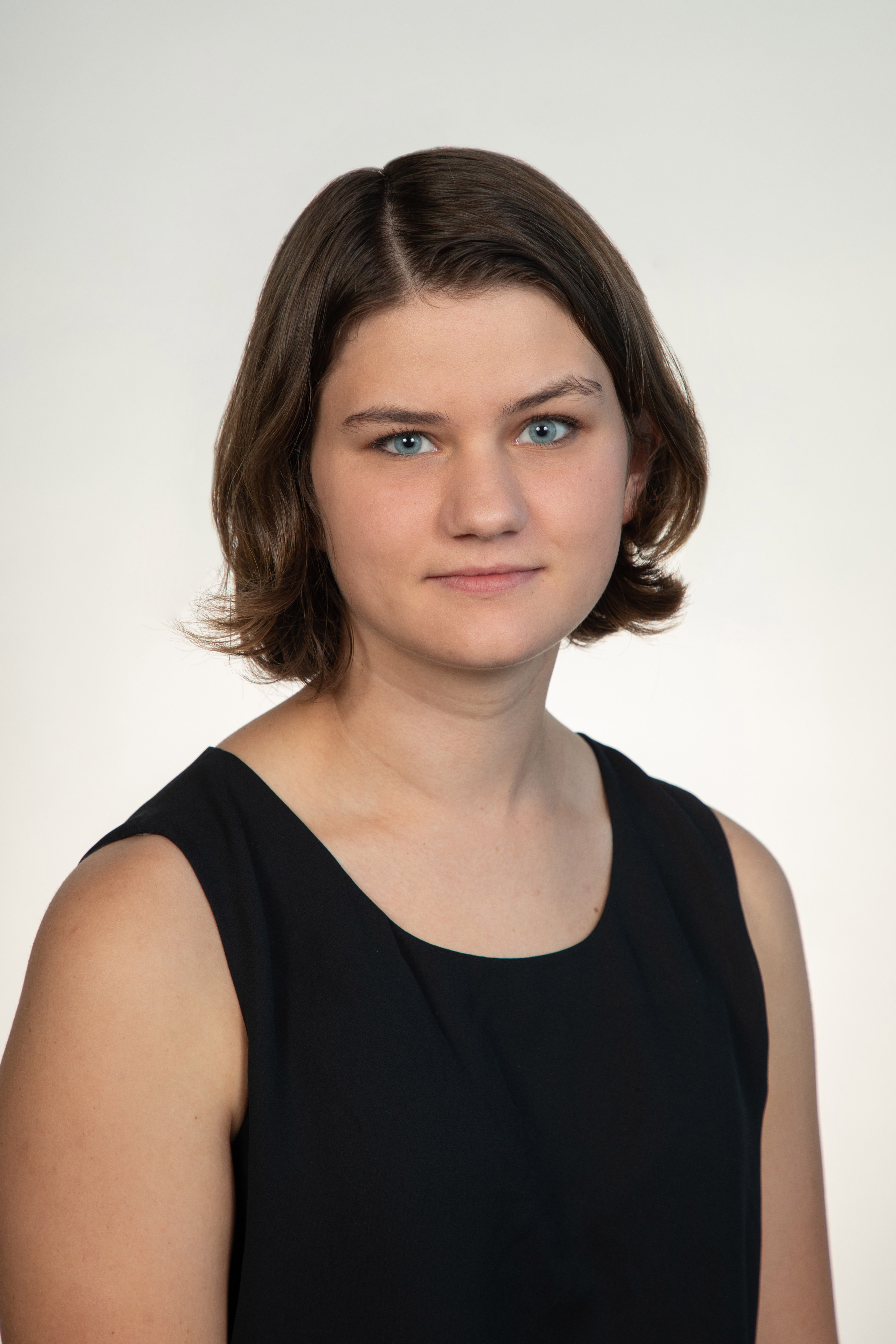
Emily Groth
Assembly Engineer
Emily Groth is a senior in Mechanical Engineering specializin in Aerodynamics. Emily is pursuing a career in the defense sector and a master's degree.
emg19d@fsu.edu
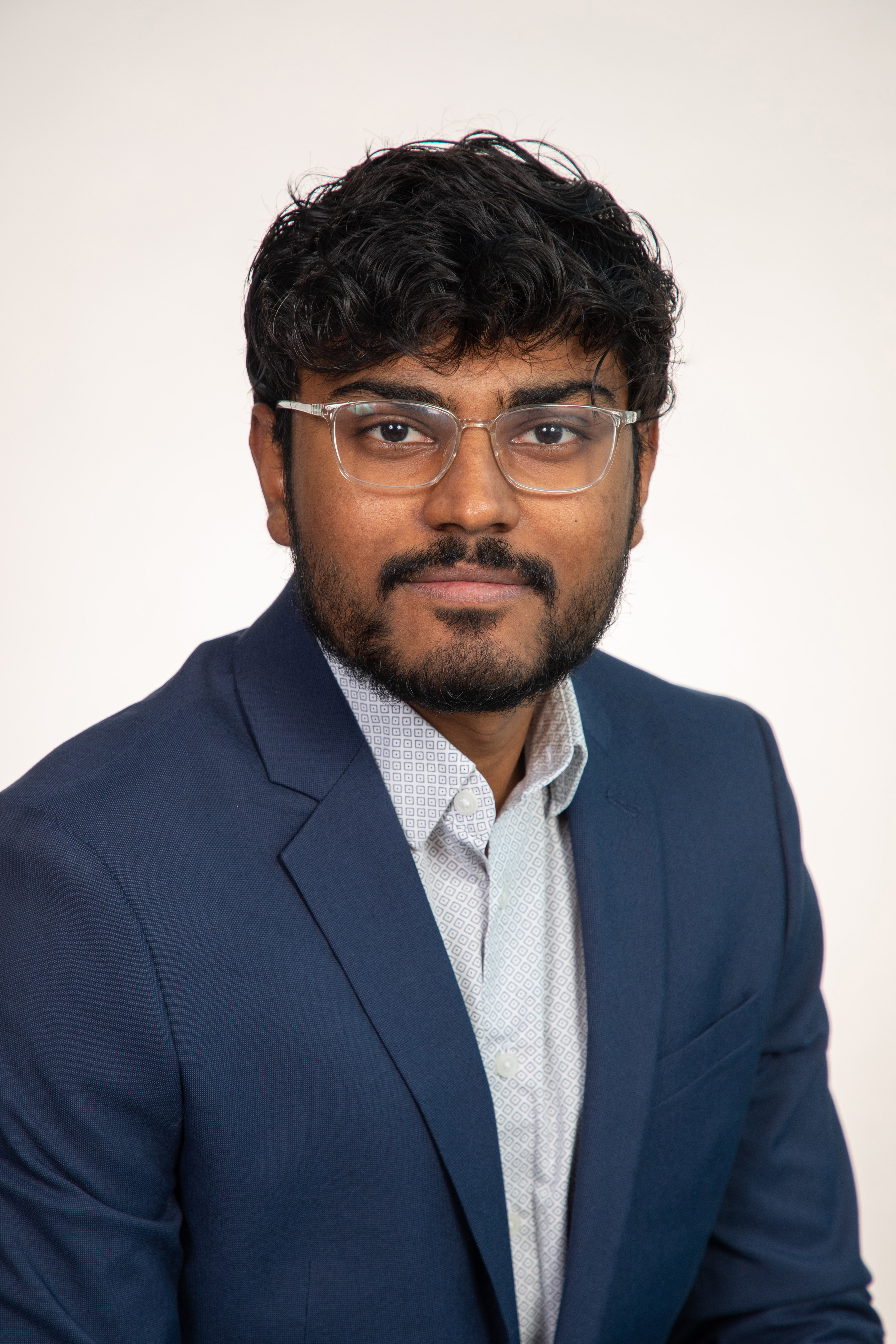
Deepkumar Patel
Design Engineer
Deepkumar Patel is a senior in Mechanical Engineer looking to persue a career in the aerospace industry. Deepkumar focus was developing the CAD model of this project.
dkp18@fsu.edu
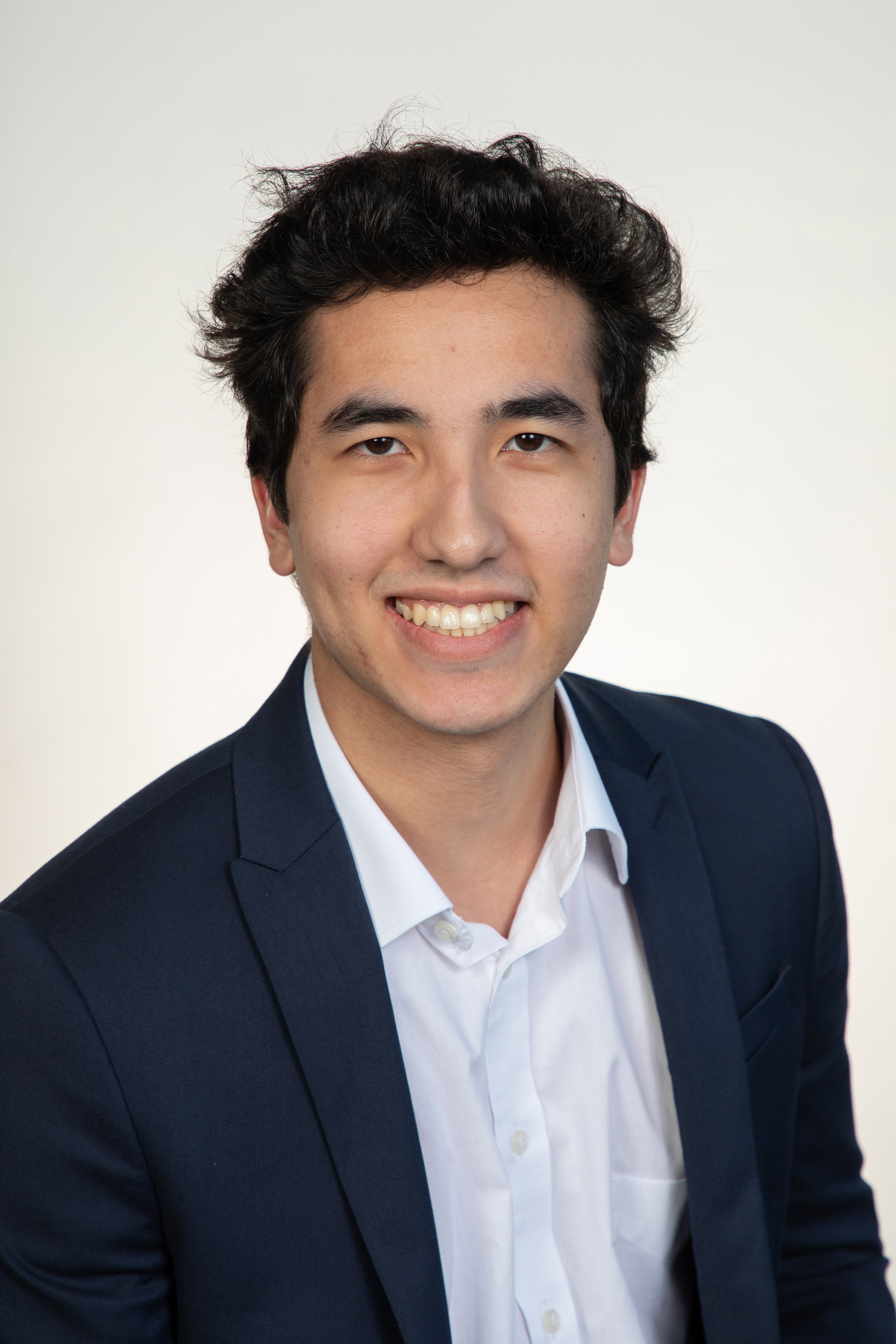
Aaron Weingarten
System Engineer
Aaron Weingarten is a senior in mechanical engineering planning to pursue a career in the aerospace industry. Aaron focused on designing and implementing the deflectable fins for this project.
apw18e@fsu.edu
Sponsor and Advisor
Sponsor
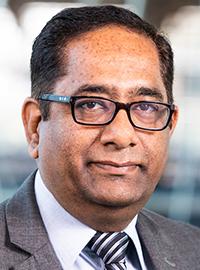
Rajan Kumar
Director, Florida Center for Advanced Aero-Propulsion (FCAAP)
rkumar@fsu.eduAdvisor
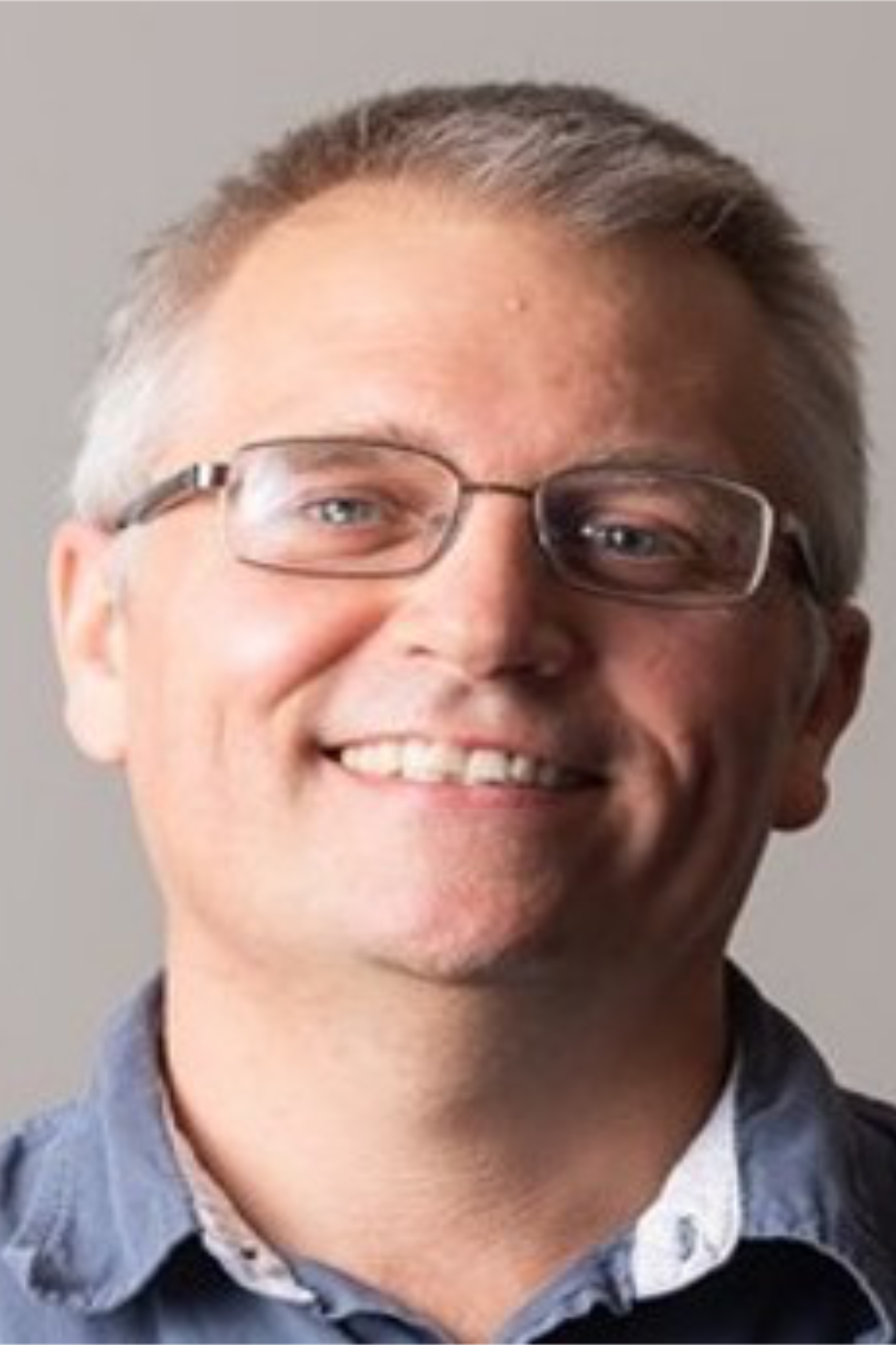
Jonas Gustavsson
Research Faculty
jgustavsson@fsu.eduAdvisor
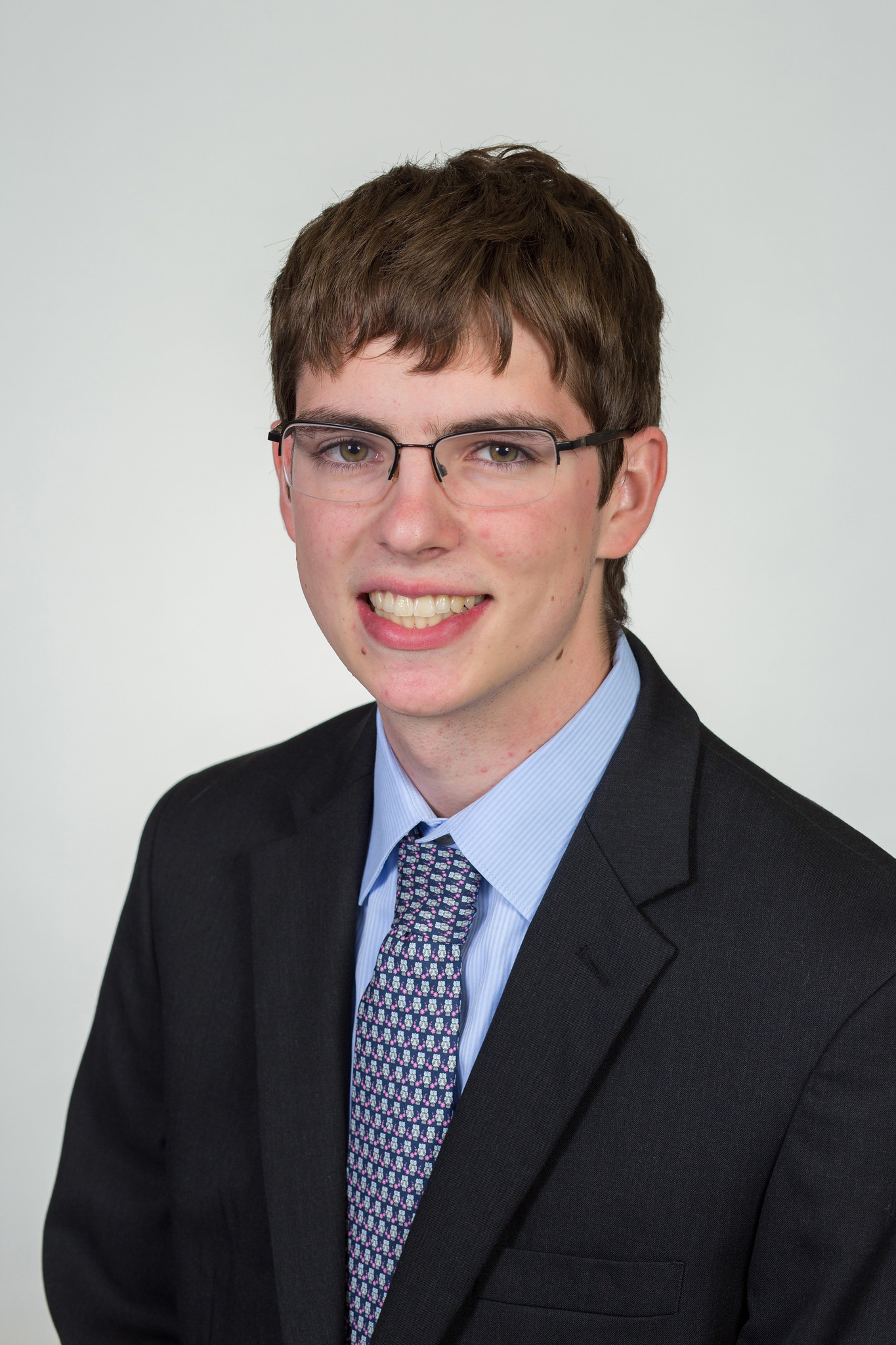
Robert Smith
Research Faculty
rsmith17@fsu.eduDeliverables
The following deliverables provide an overview of the crticial parts of our project. The evidence manual is a catalog containing numerous items such as the project scope, customer needs, functional decomposition, targets catalog and summary, concept generation, and our second semester project plan.
"Click on the title to download the document"
Photos
- All
- Projectile
- CAD
- Experiment
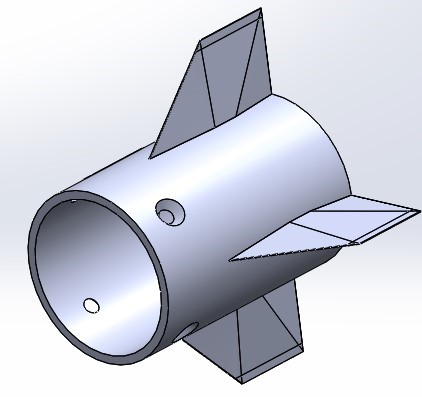
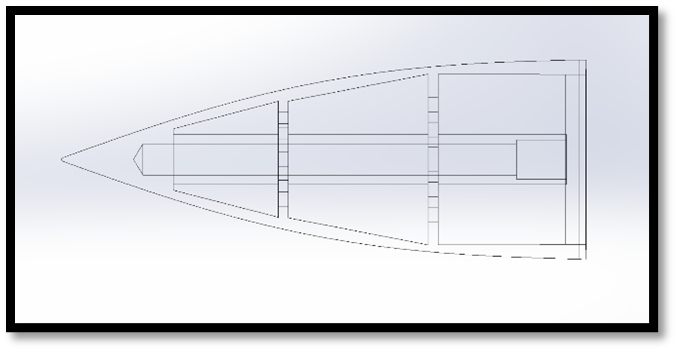
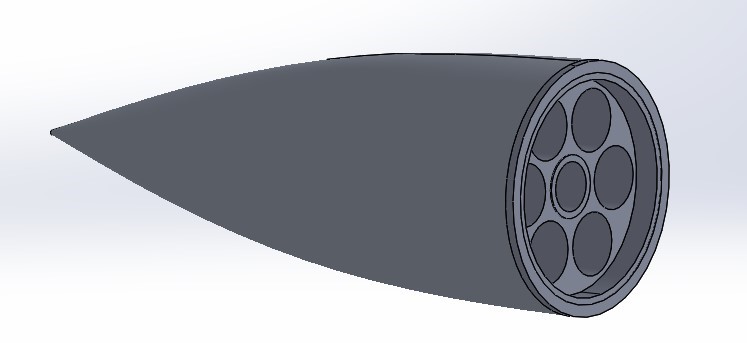
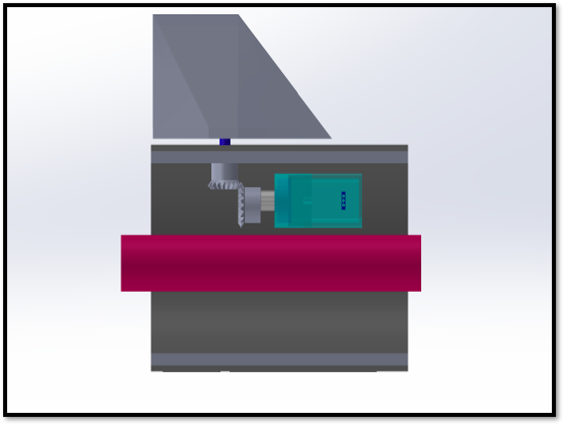
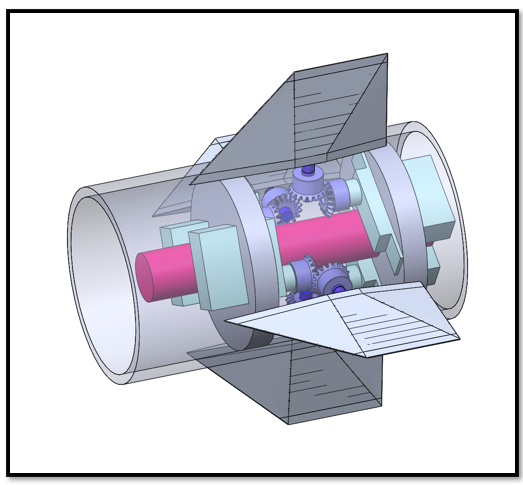
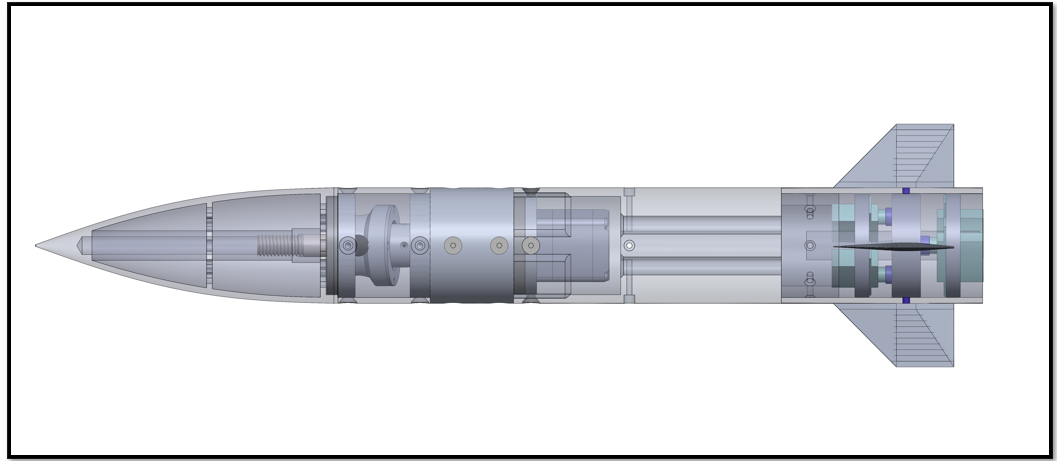