Overview
A brief description of our project
Motive for Project
Pyrotechnics are used for tasks such as rocket separation, pilot ejection, airbag inflation, and payload deployment. The vibrations from these exlosive events can be damaging to sensitive electronic devices. Because of this it is important to simulate pyrotechnic shock to gain a better understanding of the paramters that effect it and in turn ensure the safety of vital electronics. Some important things to understand about simulating pyrotechnic shock are:
- It involves high frequency short duration impacts
- There are high acceleration forces in the thousands of G's
- These things make the test sensitive to minor changes making consistancy and repeatability hard to achieve
Technical Information
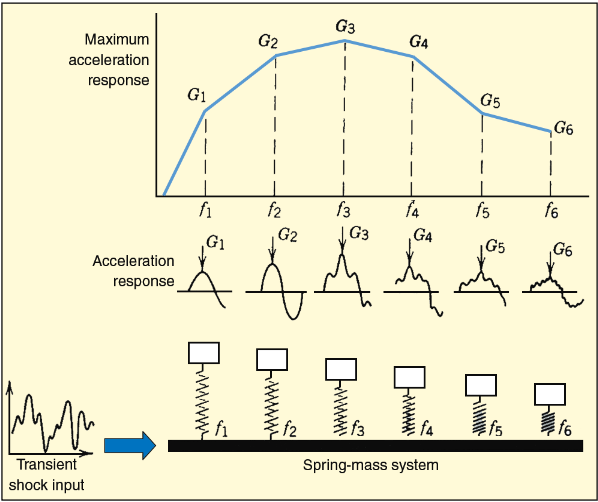
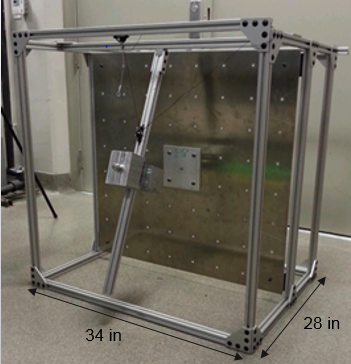
Below on the left is an example of a raw acceleration vs time plot that is recorded by the accelerometer. From here a MatLab code is used to extract the peak acceleration and plot it against the various natural frequencies resulting in an SRS curve like the one shown below on the right.
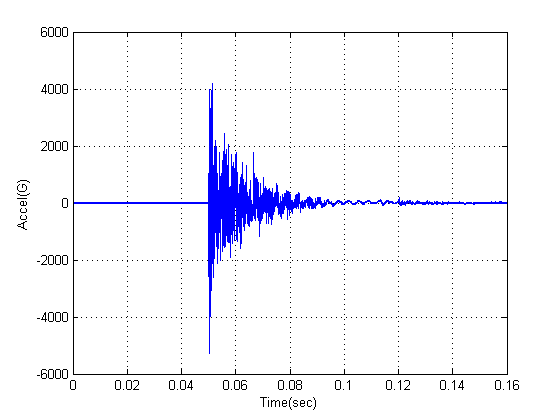
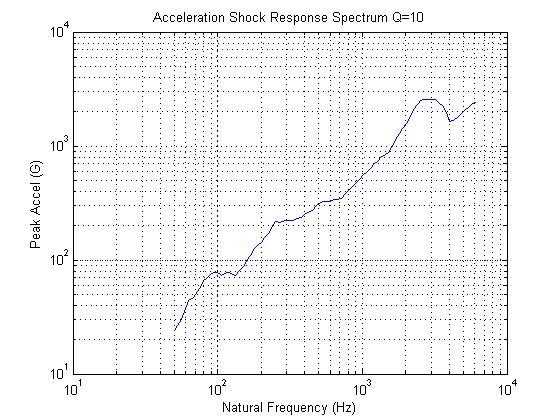
Results of Project
Much of our project entailed the pursuit of repeatability. To achieve repeatability a few changes were made to the test apparatus. First the apparatus was anchored. Anchoringreduced a significant amount of noise previously shown in the results and provided a consistant foundation. The apparatus was mounted to a large instrumental table located in the college's Mechatronics Lab. Below are two gifs one before anchoring (left) and the other after anchoring(right). Notice that the entire apparatus movies nearly an inch when un-anchored, while it is perfectly stable after anchoring.
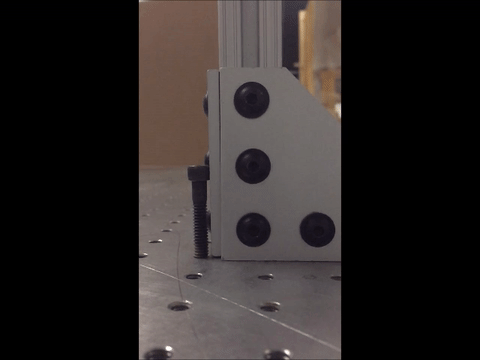
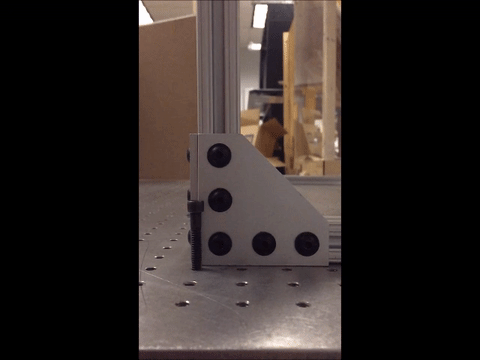
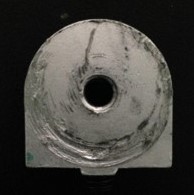
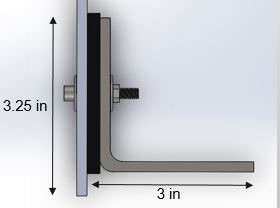
Finally after trial testing it was determined that more accurate results were achieved if the acceleromter were mounted directly to the plate instead of using a mounting plate. This left us with the final set up pictured below.
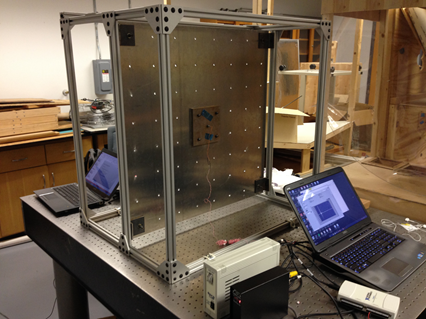
Through the process of adjustments to the apparatus repeatability steadily increased. All of the tests were run with the same parameters that included hammer at center location, sensor at center location, and hammer dropped from 90 degrees.
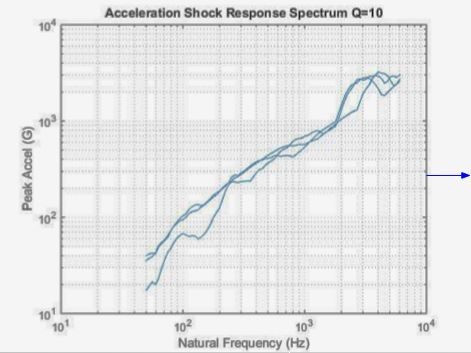

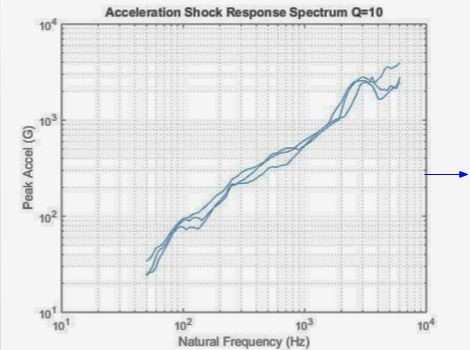
Once repeatbility was checked off, variable testing could begin. The main variables to be tested were strike location and sensor location. A grid layout was created for reference of locations, the grid is viewing the plate from the side of the hammer.
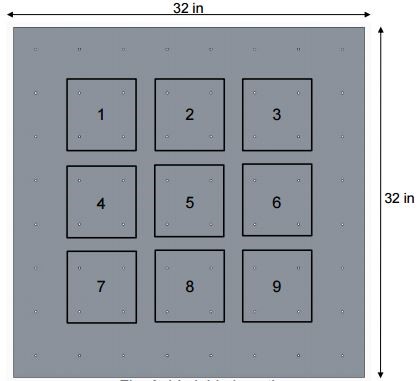
All locations have been tested by moving the strike location and also the sensor location. Below are images of strike location at points 4 and 6. More info on the results can be found in the deliverables.
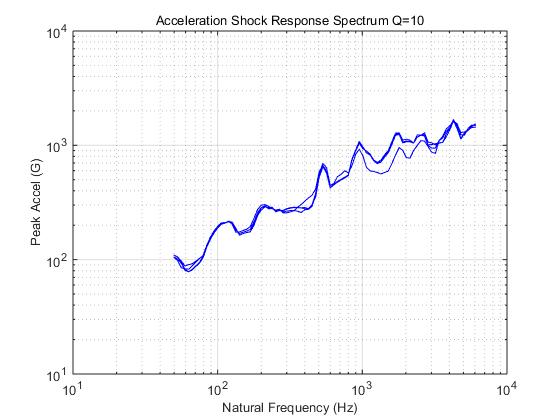
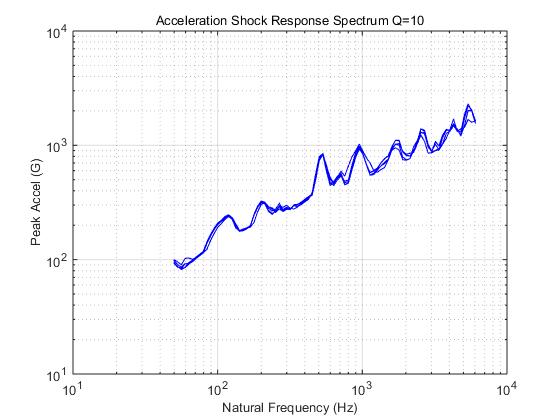