THRUST STAND DESIGN

Structure
The structural system is designed from 304 Stainless Steel to prevent corrosion from propellant leakage. It consists of 10 parts, 9 of which are unique, all secured together using #10-24 screws. Each structural component is fabricated from 0.5-inch stainless steel plating through a combination of water jetting and CNC machining. The assembled structure mounts onto a 0.5-inch stainless steel baseplate using ¼”-20 bolts, enhancing overall rigidity and optimizing natural frequency characteristics. Internal supports further increase modal frequencies.
Measurement
The main linkage is fabricated from a 304 stainless steel bar to prevent corrosion from propellant leakage. A counterweight is used to always keep the thruster assembly in contact with the thrust sensor. For force sensor functionality, an amplifier (24V) and WIKA force sensor are connected to the A0 pin on an Arduino Uno R4 Minima microcontroller and read at a 14-bit resolution.
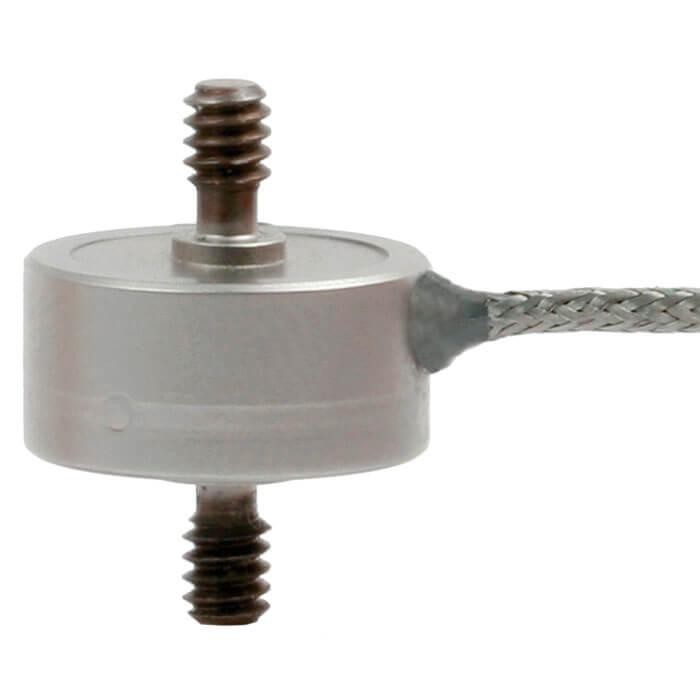
Model F2221 Miniature Force Transducer
© 2025 WIKA USA

Calibration
On one side of the main linkage bar, a slot was milled out to place a counterweight. This weight will be used to always keep the thruster assembly in contact with the thrust sensor. Once the linkage is contact with the sensor, the signal will be zeroed. Once the signal is zeroed, a known weight will be applied to a hook located on the same side as the counterweight. This will be used to establish a calibration relationship between force and voltage output.