|
Investigation of Impact Factors for Permit Vehicles |
The objective of this research is to study the dynamic interaction between heavy vehicles and highway bridges. Current research focuses on two main parts: 1) the analyses of two models of bridges with AASHTO Type II and IV Girders, and 2) the effect of the bouncing cargo on the bridge dynamic response. The effects of surface imperfections in the bridge approach are included on the bridge models to simulate real life conditions. Several different bridges around North Florida were surveyed and two of these were selected and FE models were developed. The LS-DYNA parallel code is being used to perform the numerical simulations.
|
Selection of Permit Vehicles and thier F.E. Models |
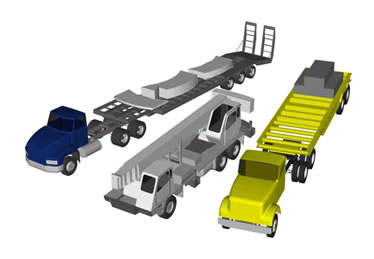
|
Three permit vehicles were selected for FE modeling. They included: Mack CH613 truck tractor with a three axle single drop lowboy trailer, a Terex T-340 crane, and the FDOT tractor-trailer, as shown in Figure 2.14. Mack is a popular tractor trailer with GVW (per FDOT records) exceeding 200,000 lbs. Fortunately, its total mass is well distributed through six axles, twenty two tires, and is supported by well-designed spring suspensions and shock absorbers. Although the Terex crane has a smaller GVW, it is supported by only three axles with a smaller bridge distance (i.e. a distance between the two most distant axels), which ignited the FDOT interest in this vehicle. Finally, the FDOT truck was selected due to its very stiff (almost non-existent) suspension. The vehicle models developed are small and computationally efficient. Each consisted of less than 25,000 finite elements. In addition to rotating and pressurized tires an emphasis was placed on correct characterization of the spring and damping properties of each suspension. |
Selection of Prestressed Reinforced Concrete Bridges and thier Model Development
|
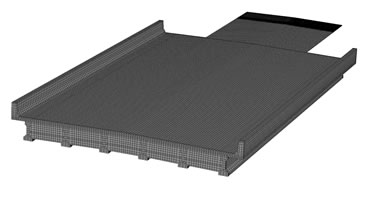
|
A broad class of smaller, popular, prestressed, reinforced concrete bridges was selected for this research. Three of these bridges, made of AASHTO type II, III, and IV were selected for modeling and analysis, as shown in Table 1.
Table 1. Dimensions of one span of each bridge
Bridge
# |
AASHTO
girder type |
Number
of spans |
Span
length [m] |
Span
width [m] |
540074 |
II |
2 |
12.1 |
11.6 |
500133 |
III |
3 |
21.0 |
13.1 |
590056 |
IV |
3 |
29.1 |
12.6 |
Each model included such elements as: AASHTO girders, concrete deck, diaphragms, bridge barriers, elastomeric bearing pads, and a bridge approach. Most of the parts were modeled with linearly elastic 8-node solid elements with concrete properties as tested. Bridge reinforcement was modeled using 1-D beam elements with nodes shared with the nodes of the adjacent concrete elements. A complete, typical FE model of the bridge span consisted of 145,604 finite elements. |
AASHTO Dynamic Load Allowance Factors
|
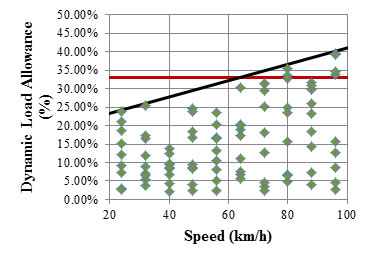
|
Dynamic load allowance (DLA) factors were calculated for all bridges depending on vehicle types and their velocities. DLAs were determined based on maximum displacements and strains using data from experimental testing and from computational analysis. Strain based DLA factors came out to be more reliable, closer to experimental data, and to values recommended by AASHTO
AASHTO recommendation of using DLA=33% was found reasonable yet conservative for smaller speeds. For higher speeds, an upper bound of DLAs can be approximated as:

Several features were identified as triggering significant DLA. They included: surface imperfections (as abutment joints and bridge approach depression), loosely attached cargo producing so called hammering effect, and characteristics of the vehicle suspension. |
|
|
|