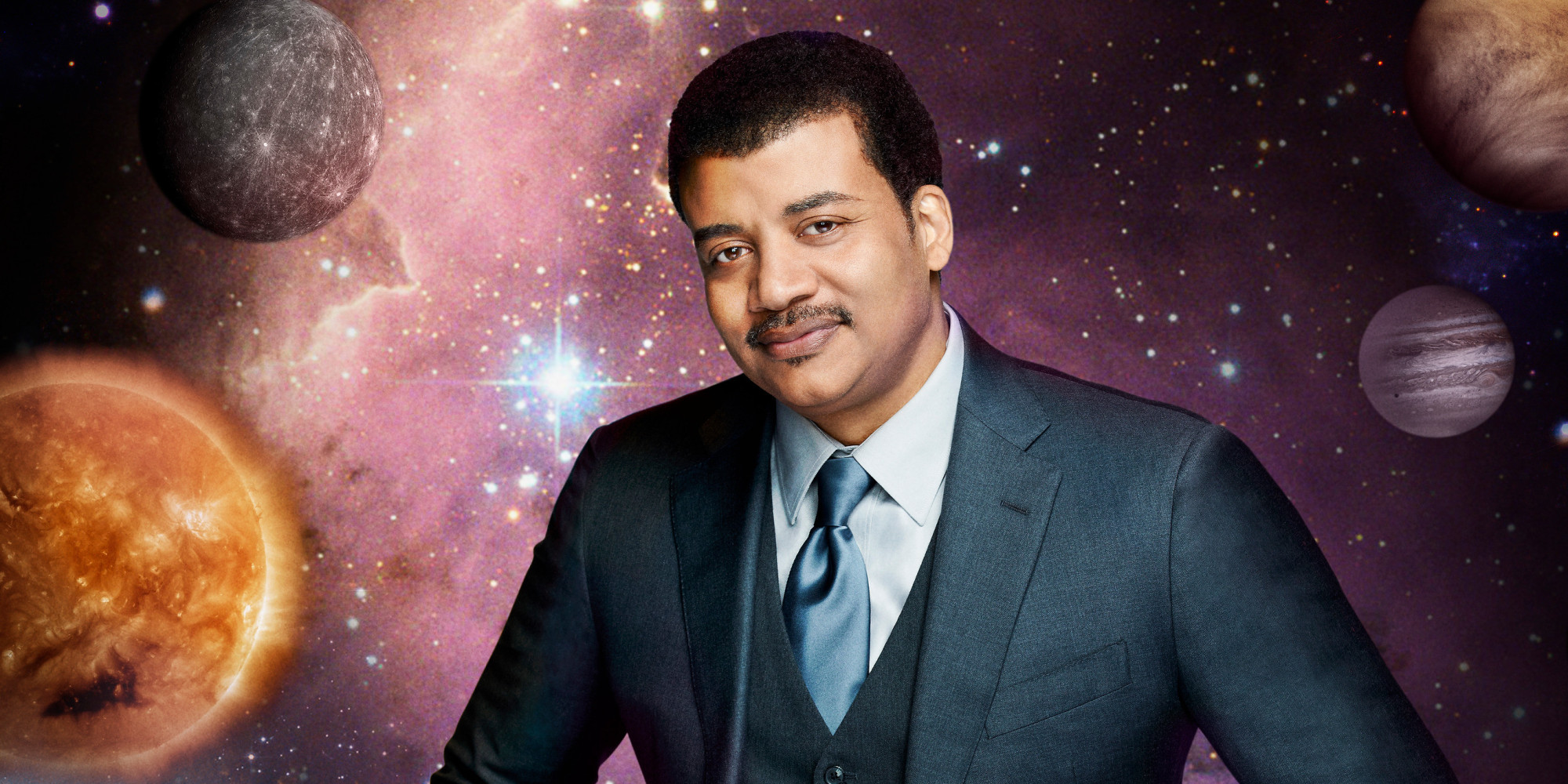
How We're Going to Solve It
A quick abstract of our project to show how we're approaching the solution.
All space missions require rocket engines to propel the payload to complete the desired objective. These fuels are usually liquid. Since the density in liquids is higher than gas form more propellant can be fit in the tanks. To keep the propellants in liquid form they must be kept in a pressurized tank and at very low "cryogenic" temperatures. The common way to keep the liquids cool is to create a vacuum around the tank to prevent convection from allowing heat in. However, this doesn't help with radiation as radiation doesn't need a medium to travel through.
This is where the MLI (Multi-Layer Insulation) comes in. MLI is a stack of aluminum-foil looking sheets that are separated by a thin mesh about a millimeter thick. This insulation acts as a shield against incoming radiation. The problem arises when, since the MLI is in the vacuum portion of the tank, residual gas gets stuck in-between the layers of Mylar. The residual gas is detrimental to the insulating qualities of the tank. In order to observe how this takes place, NASA Marshall Space Flight Center would like a sensor that can sense very strong vacuum and is small enough to fit between Mylar layers.
This is no small task... click the link under "How We're Going to Solve It" to read our Abstract.
A quick abstract of our project to show how we're approaching the solution.
Click the link below to see our report and presentations detailing our project solution.