Overview
Our project is to design a radio-controlled cargo plane for the Society of Automotive Engineers (SAE) Aero Design Competition. This project is a two-team project. We are the Aero-Propulsion team. The second team is the Geometric team. We focused on design features and calculations for the plane during flight. Our goal is to complete the flight path while keeping a stable flight with a cargo load. We used the project to test a new design by adding a canard. It is a smaller wing in front of the main wing that produces lift. The plane is about 4 feet long and has 3 wings: the canard, main wing, and tail. The main wing has the largest surface touching the airflow. This means our main wing produces the most lift. Planes with two wings are hard to fly. However, we found that adding a tail made the plane more stable. The tail features a T-tail design, where a vertical section holds the tail wing in a plane above the main wing. We placed our cargo bay between the canard and the main wing. This allows for easier loading and unloading of cargo. Our plane can resist crosswinds up to 30 miles-an-hour, making the plane stable during landing. The plane produces a maximum thrust of 222 pound-force. We calculated performance of our plane during takeoff and landing to figure out our plane needs at least 360 feet of runway space to work. Our plane can carry a maximum weight of 11 pounds. We use servomotors to move control surfaces. Our plane works under large forces with the servos we selected. This design shows that a canard wing plane can create stable flight with a cargo plane.
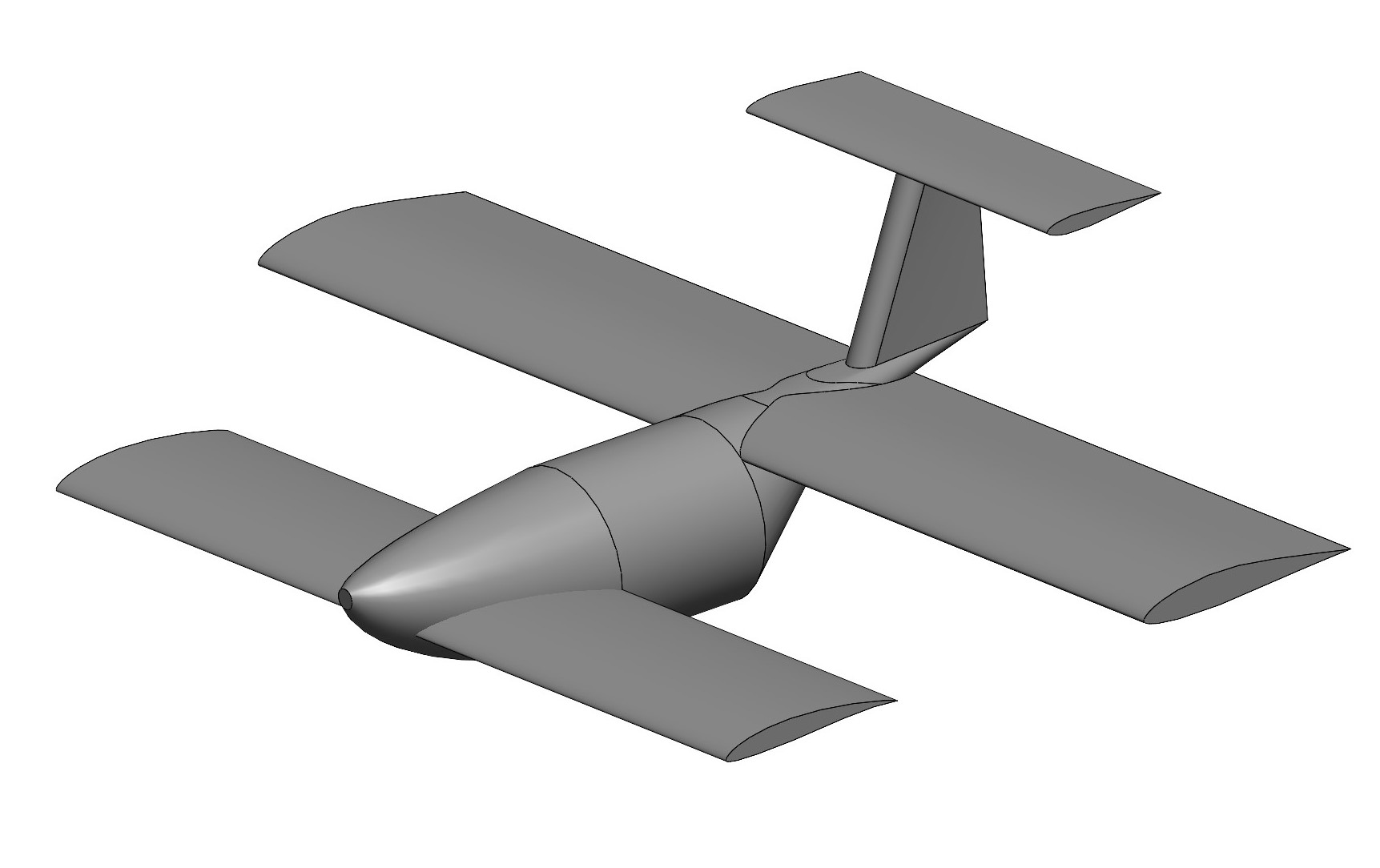
Validation
To validate our design we used multiple Computational Fluid Design (CFD) analyses to visualize flow around the wings. We used programs such as Xfoil, which is a program that uses an airfoil’s shape as well as the atmospheric conditions of the flight to analyze performance. Using 200 points around the airfoil, the program can create a multitude of graphs to determine how the wing would react under different circumstances. CFD was performed using the flow simulation toolbox in SolidWorks. To simulate this, the model was put to have a wind velocity of -440 in/s (about 25 mph, which is the plane takeoff speed) going toward the nose of the plane.To simulate the plane with varying AoA some trigonometry calculations were done to vary the vector of wind speeds that would be affecting the plane in the angle needed. After refining the mesh as much as possible and running the program cut plots were made to visualize the airflow and view the vorticity and turbulence around the fuselage and the wing profiles such as pictured below.
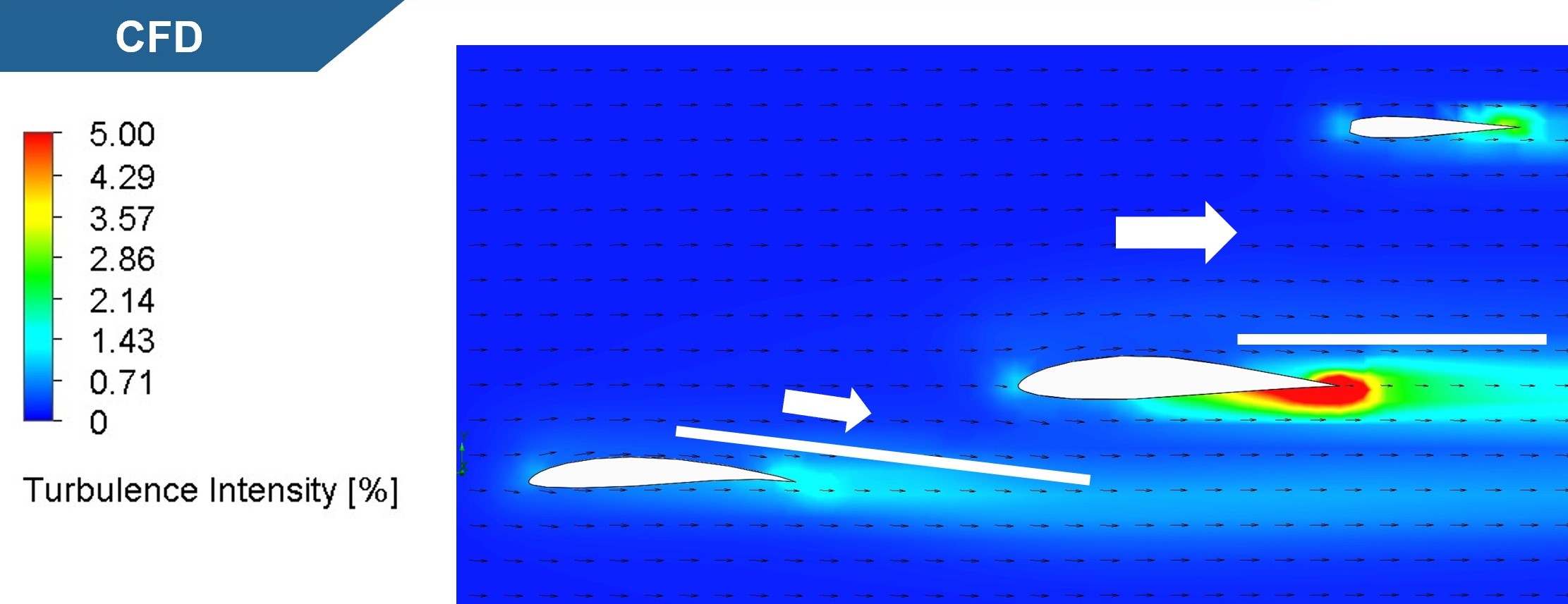
After running countless simulations we figured that we would need physical validation as well as simulation. for physical validation we ran a series of wind tunnel tests to verify that our simulations were correct, at least quantitatively. Smoke images taken for various angle of attack values. They show streamlines (airflow lines) around the wing. With the equipment available to us at the FCAAP sub-sonic wind tunnel, we had to select a small region for the smoke flow study as the laser beams had to be focused to a certain region. A video of the test being conducted and an image of the flow visualization are included below.
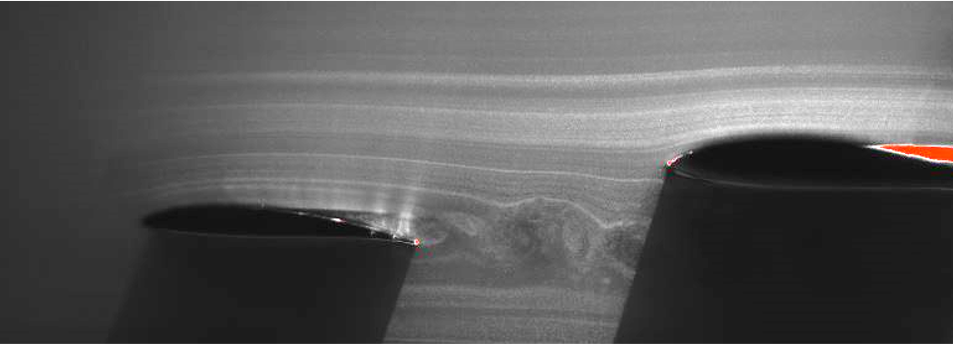
Final Design
The geometric integration of the project fell under the capable hands of Senior Design Team 508, but because they were short handed, being a team of three while we have five, we also helped them with whatever they needed as they did for us whenever we needed it. That being said, we helped design the control surface movements using a gear and belt system to move the ailerons, elevators, and rudder. The main wing CAD is pictured below.
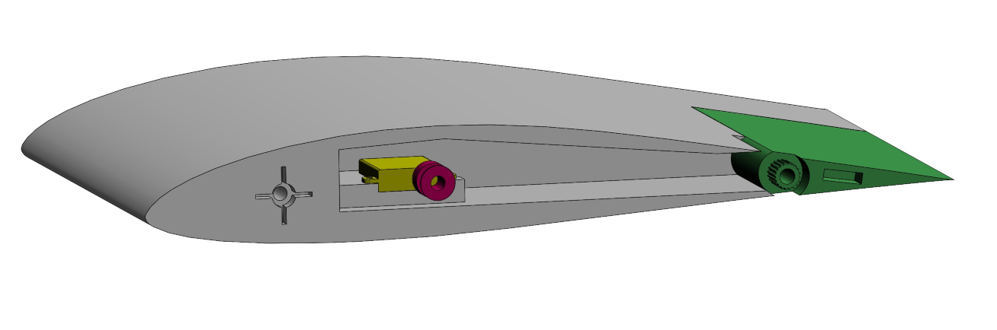
After two semesters of work and countless hours sacrificed by Teams 507 and 508 the final physical 3D printed plane is pictured below!
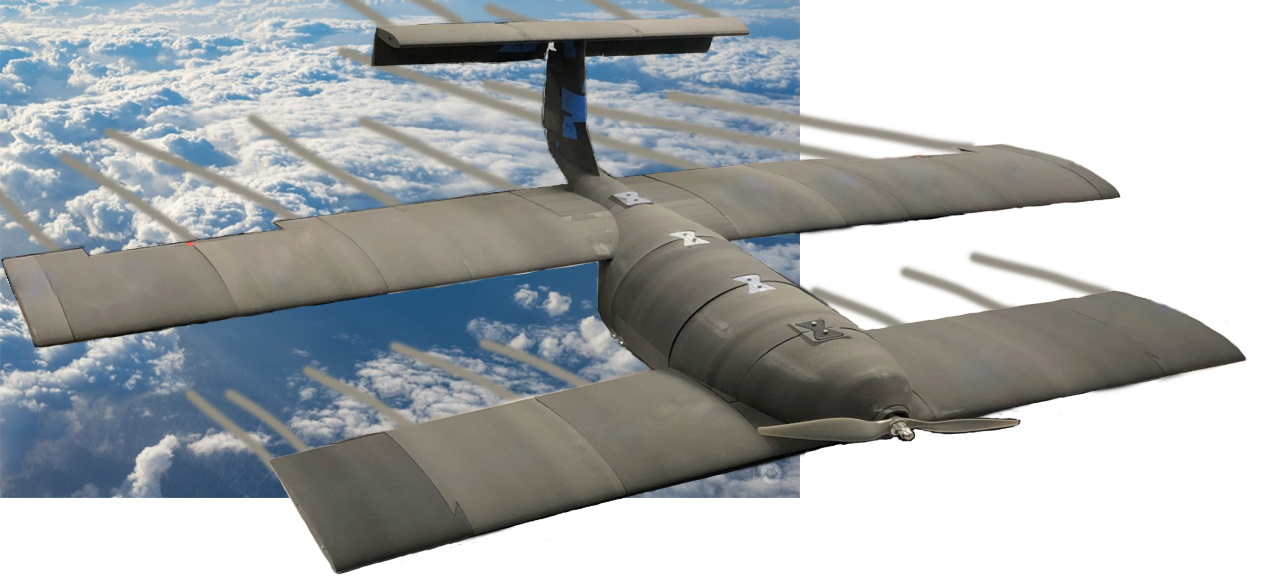