Abstract
Due to an incident that occurred because of a faulty and outdated testing method, Florida Power and Light has come seeking a more accurate and objective solution to pole health examination. This project’s objective is to create a robot that can climb wooden power poles and find out if the pole is safely climbable. This is a joint venture between mechanical and electrical engineering teams. The mechanical engineering team handles the design of the robot and its climbing and the electrical engineering team deals with the sensing.
The current pole safety test is the hammer test. It relies on a line worker listening to the sound the pole makes when struck to decide the integrity. The Florida Power and Light Robotic Pole Inspection Collar will use ground penetrating radar (GPR). This sensor creates a more accurate test by studying the internal quality of the pole. Testing the robot on both healthy and unhealthy pole samples calibrated the ground penetrating radar.
The robot conforms to the pole using a triangular prism shaped design. This design allows simplified mounting by being able to wrap around the pole. The robot relies on tension and its shape to keep contact with the pole’s round surface. This design uses motors to cause vertical motion while its passive wheels help keep grip on the pole. The wheels of the robot were custom-made by using two cones to form an hourglass shape to provide improved grip on the poles by having two points of contact. The driven wheel also has a rubber coating with spikes to further increase grip. The robot houses the ground penetrating radar between the two triangles where it can contact the surface and send pulses to scan for flaws in the wood.
Iterations
Months
Team Members
Final Design
Final Design
The robotic pole inspection collar is a device that has the potential to replace the OSHA hammer test. The final product was a result of several early issues discovered from rapid prototyping being solved across multiple iterations of the robotic design. The final design demonstrates the robot’s ability to scale utility poles while providing space for sensor technology that is implemented to determine pole health.
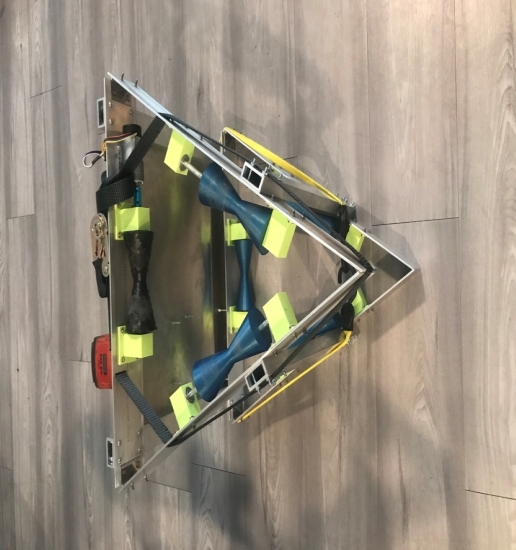
Prototype Iterations
The FPL pole climbing robot has the capability to safely traverse a utility pole prior to a lineman climbing it. The final product was a result from serval early issues discovered from rapid prototyping that were solved across multiple iterations of the robotic design. Pictured below are the sequential iterations of our selected triangular design that lead up to the final design. The final design demonstrates the robot’s ability to scale utility poles, while providing space for sensor technology that is implemented to determine pole health.
Pole Climbing Robot Test Run
This video depicts the FPL pole climbing robot ascending and descending the pole. The robot mounting process takes about a minute and the robot takes approximately 13 seconds to climb the pole sample to the top and return to the bottom. This is a quick run where the robot is preprogrammed to climb to the top of the pole and then descend back down to the ground. A bluetooth module and iOS interface were initially going to be configured with the robot to allow the user to directly interact and select heights for the robot to climb to.
Team Members
Department of Mechanical Engineering
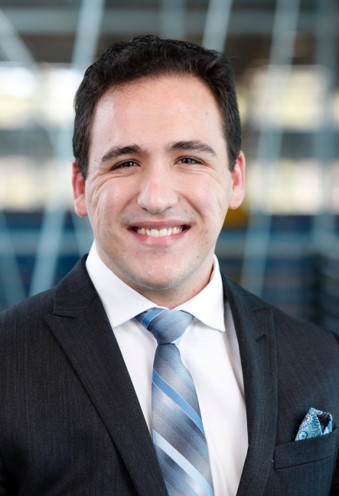
Angelo Mainolfi
Project Engineer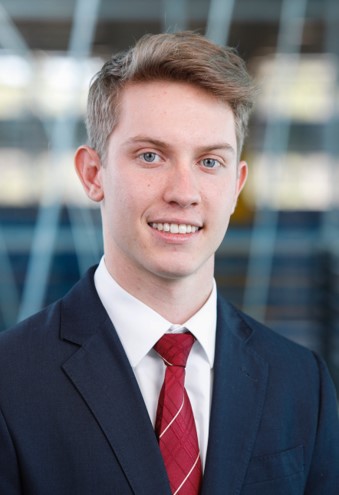
John Flournoy
Design/Materials Engineer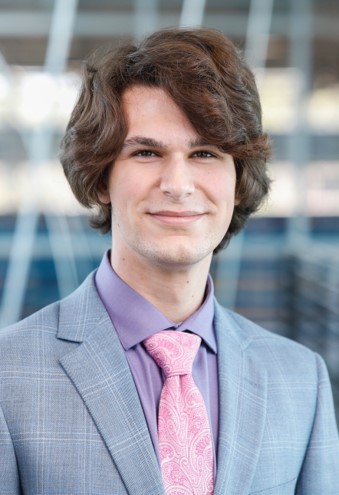
Carey Tarkinson
Mechatronics Engineer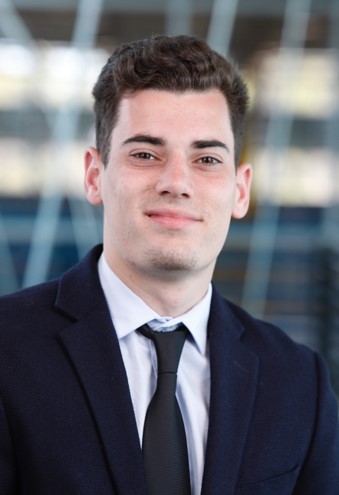
Mathew Crespo
Mechanical Syatems EngineerDepartment of Electrical and Computer Engineering
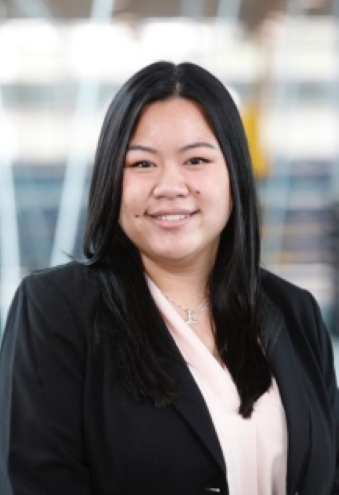
Corie Cates
Project Engineer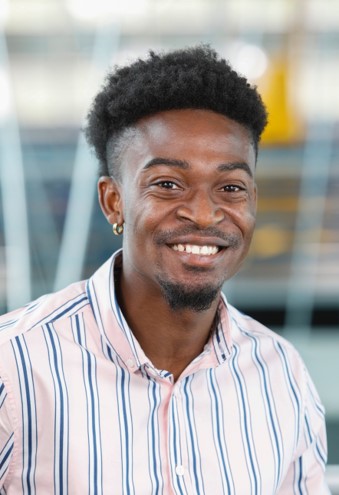
Alonzo Russell
Hardware Engineer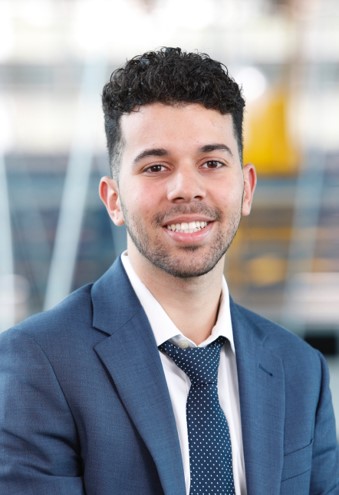
Leonardo Vazquez
Software Engineer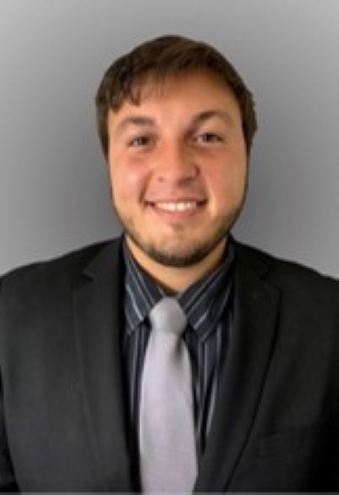
Thomas Williams
Hardware EngineerAdvisors
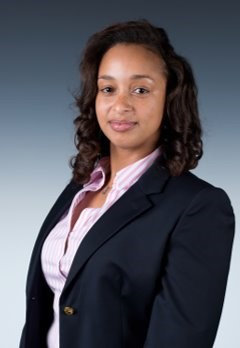
Genese Augustin
Lead Project Manager-FPL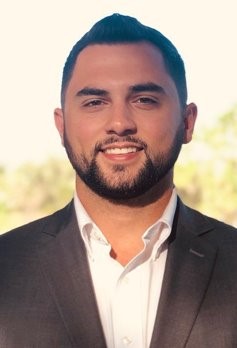
Troy Lewis
Engineer II-FPL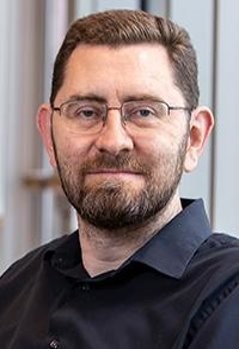
Dr. Jonathan Clark
Associate Professor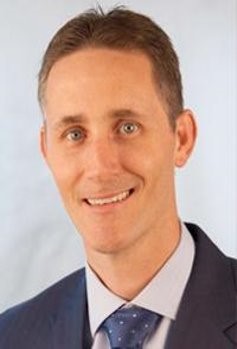