About the Project
Our Corning sponsors, Jeffery Roche and Jeffery Stott, experience unstable conditions in their plant. They are part of a company that makes ceramics to filter harmful emissions. While shorter ceramics are on the conveyor pallets, they risk falling off because of quick stops and vibrations, resulting in damage. The way that Corning corrects this issue lowers the risk of pieces falling but needs extra labor. Ceramic cylinders moving down the conveyor need to keep their faces bare for quality testing. The plant has various constraints that our design can’t interfere with. The team created a mechanical lifting design that will combat the unstable conditions in the plant while lowering the need for extra labor. Inspiration for the design’s look came from the shape of a T, our team has named the design the “Self-nesting T’s.” These Self-nesting T’s raise and lower on both sides of the ceramic faces. The design uses no grease and relies on shoulder bolts to move. Considering the dust present in the plant environment, standard grease won’t work. To engage, the design uses overhangs placed along the conveyor to lift and drop the T’s when needed. Our T’s go low enough so the ceramic faces will uncover during testing. The light materials selected allows the design to move with less forces needed. The motion of the design allows it to fully integrate with factory conditions. This range of motion protects the ceramic and brings down the labor cost. Adding thin foam padding prevents further ceramic damage. Various tests confirmed the design’s ability to perform its goals. After senior design day, Corning can adjust the design and apply it in their factory to reduce their labor costs while protecting the ceramics from damage.
Keywords: Ceramics, Stabilization, Manufacturing
The Design
Self-Nesting T's
The Self-Nesting T utilizes the shape of Corning's current design while also providing autonomy. The teams’ design utilizes a set of linkages in an X-shape, which are connected by two smaller linkages. This system is raised and lowered by a gear and rack system. Utilizing a slider block with a lever connected to the Z-shaped rack allows for the rack to move, actuating the gear. Overhangs on the sides of the conveyor are used to actuate the lever that raises the system. With the utilization of a Z-shaped rack, the gears are able to move in the opposite direction which will lift the small linkages as needed.
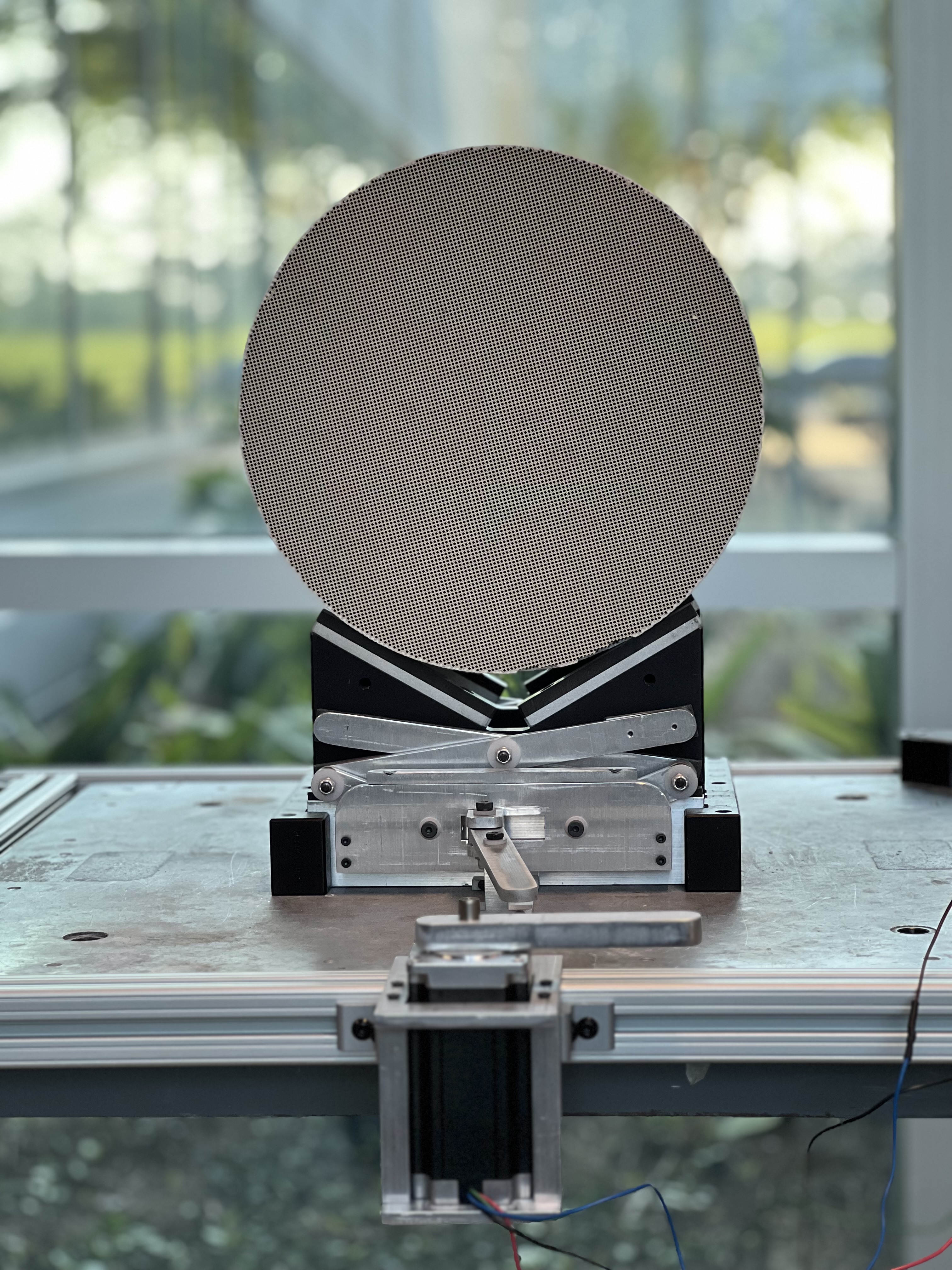
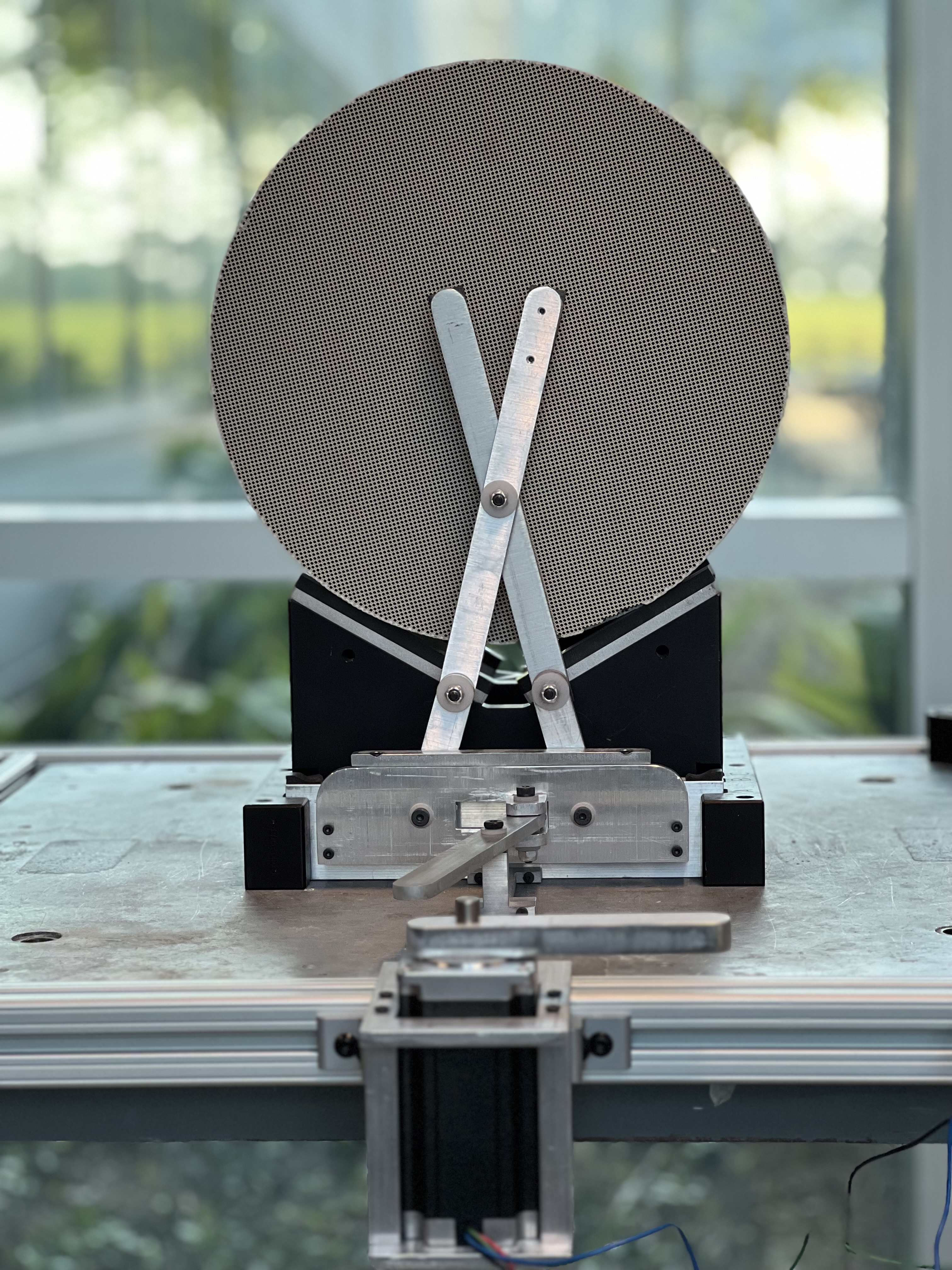
For this design, the gears are rigidly attached to the small linkages using screws. Attached to the smaller linkages are the linkages that create an X. At the connection point of these linkages, a shoulder bolt is used in order to provide a sliding joint. The two long linkages that create an X are also connected using a shoulder bolt to ensure they stay connected and can rotate as needed. All of these shoulder bolts are counter bored into the linkages to prevent them from causing damage to the ceramics.
Overhangs
The overhangs are an integral part of the team's design to ensure the autonomy of the Self-Nesting T. The overhangs are the actuation method that allows the Self-nesting T to raise and lower as needed. For the team’s testing and demonstration purposes, the design features an aluminum extrusion railing that goes around the pallet that holds the ceramics. These railings are used to secure the housing for the motors and automation center in place. The automation center will contain an Arduino, breadboard, motor drivers and a push button. The motors and motor house will be located on the sides of the pallet that contain the Self-Nesting T, while the automation center will be located on the backside of the pallet. The motors feature an aluminum slapstick secured to the shaft with a setscrew. This slapstick is used to hit the switch lever arm of the Self-Nesting T. This actuation will allow for the raising and lowering of the Self-Nesting T.
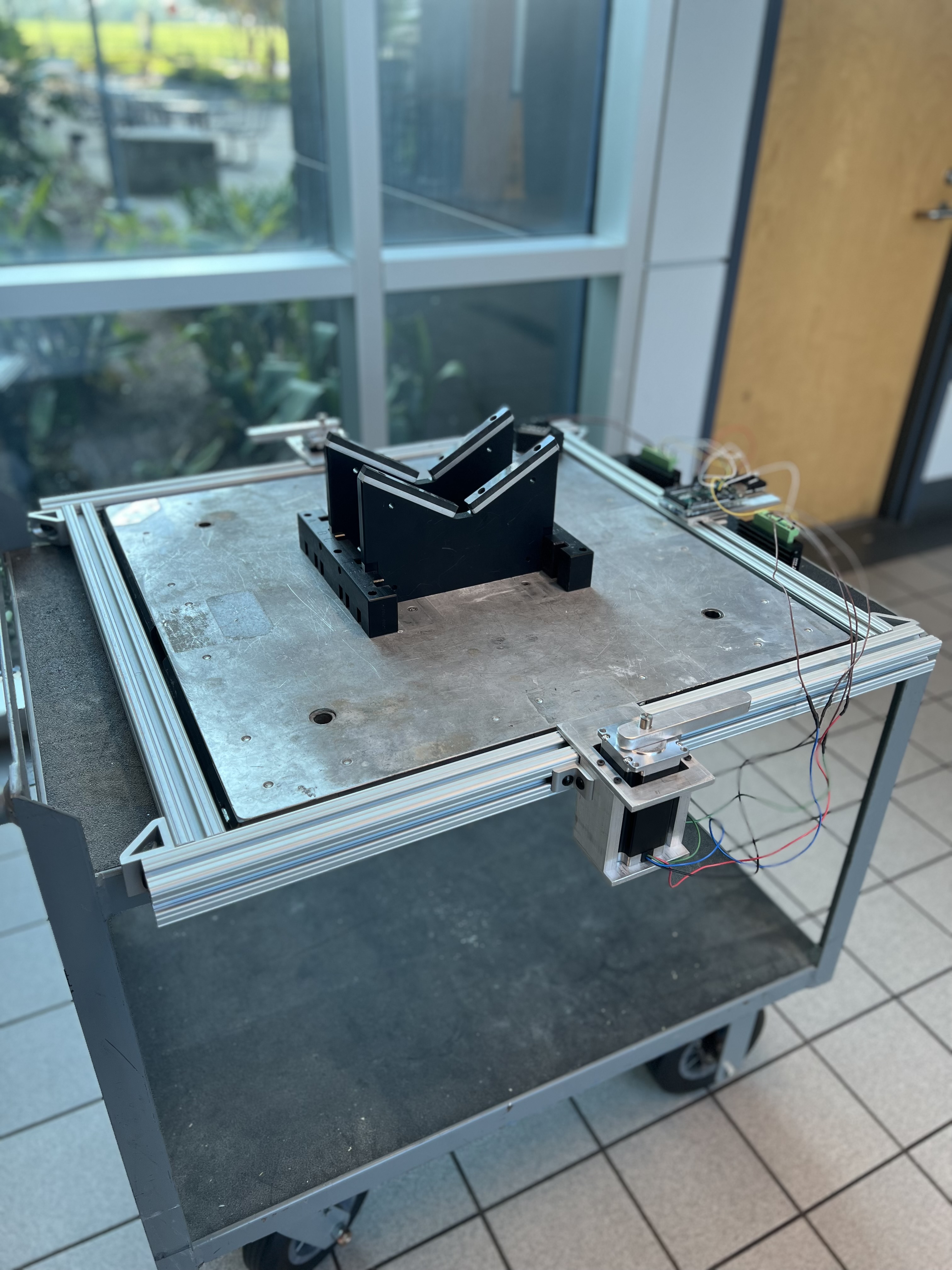
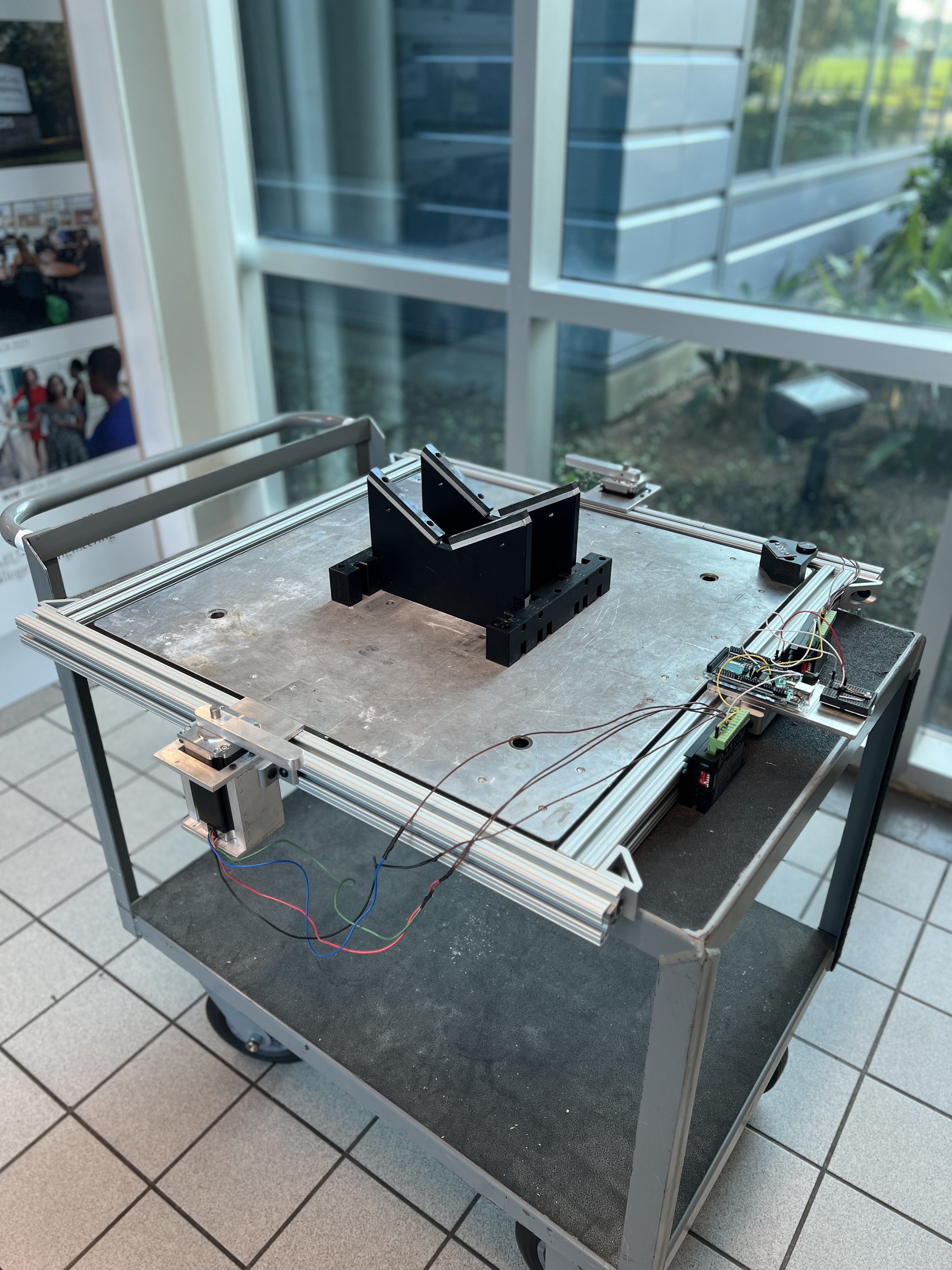
The image shown on the right shows the motor mounts and the automation center. These are the locations for the motors and all the electronics that are used to actuate the device. The automation center features two TB6600 motor drivers, an Arduino mega 2560, a small breadboard and a push button, for actuation. The Arduino is plugged into a laptop that is used for programming. The two motor drivers are plugged into the motors and into the Arduino directly. Not shown is a 48V power supply that will power both motor drivers. The motors used are high torque Nema23 stepper motors. These motors have a 1.8-degree step and can output around 3 N*m(28 lb*in) of torque. They can change their speed or torque, depending on the current or voltage being used. Each motor uses 24V of power to function. When this design is implemented into the Corning manufacturing plant the method of actuating the slapstick will be updated to work with their RFID system.
Deliverables
All of the teams submitted assignments.
Future Work
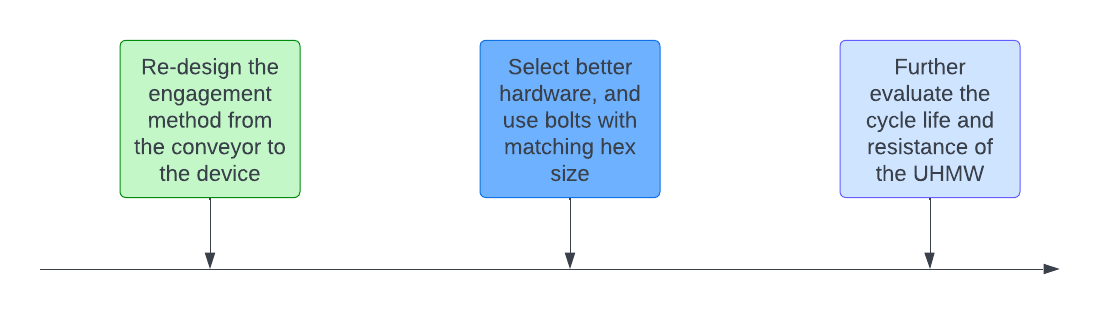
Meet Team 506
All team members contributed to the completion of the project in time for Engineering Design Day.
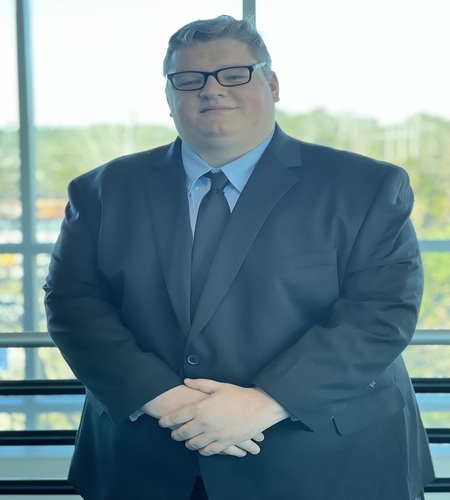
Pawel J. Grum
Mechanical Test EngineerPawel will graduate with a bachelors degree in Mechanical Engineering from the FAMU-FSU College of Engineering in the Spring of 2023. Throughout his studies, he has gained a peaked interest in robotics systems and structural analysis. He hopes to pursue a career in either field following graduation.
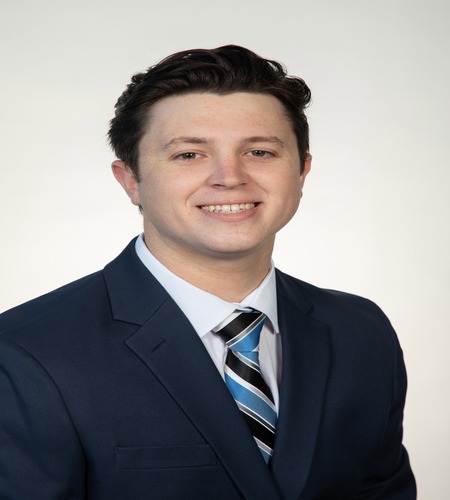
Robert C. Kosmas
Structural Design EngineerRobert Will graduate with a bachelor's degree in Mechanical Engineering from FAMU-FSU College of Engineering in the Spring of 2023. After graduation Robert plans to find a full-time job in an industry-leading company where he can begin developing his professional tools and expertise.
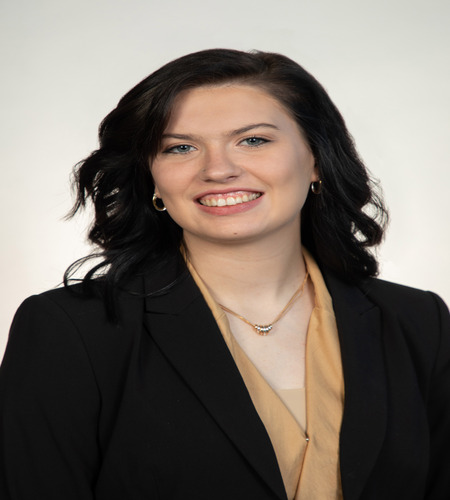
Taylor M. Larson
Dynamics EngineerTaylor will graduate with a bachelors degree in Mechanical Engineering from the FAMU-FSU College of Engineering. She will begin her job as a Mechanical Propulsions Engineer at Lockheed Martin upon graduation. She plans to return to school for her master's degree with a focus on dynamic systems and material science in Fall of 2024. She is interested in the development and improvement of prosthetic knees and feet.
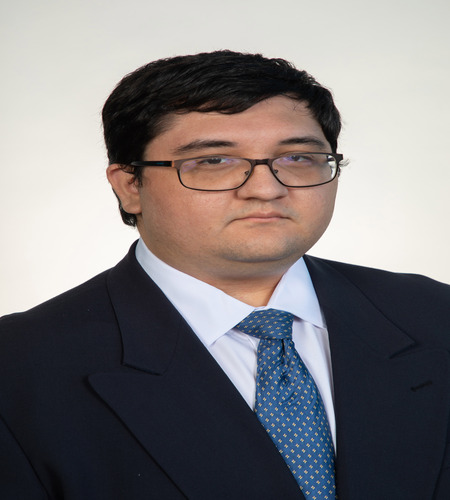
Segundo A. Sanchez
Materials Analysis EngineerSegundo will graduate with a bachelors degree in Mechanical Engineering from the FAMU-FSU College of Engineering in the Spring of 2023. He gained an interest in material science and engineering during his education and hopes to pursue a career in the material science industry after graduation.
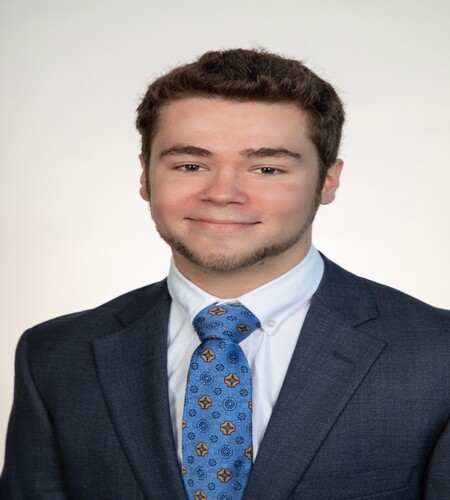
Jared T. White
Manufacturing EngineerJared will graduate with a bachelors degree in Mechanical Engineering from the FAMU-FSU College of Engineering in the Spring of 2023. After graduation, Jared will begin his engineering career in the industry. He is interested in materials, manufacturing, and mechanical systems.
Advisors
Team 506 would like to thank our advisors for their support, expertise and help with the project.
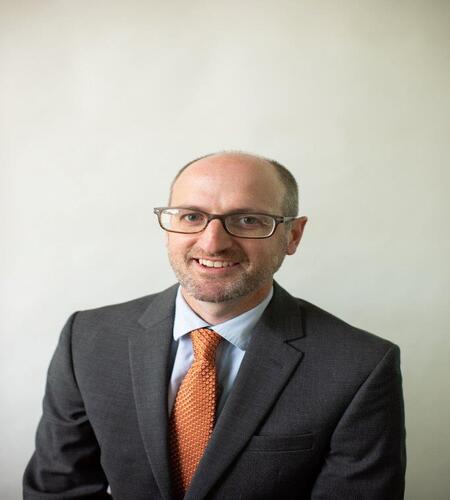
Jeffrey Roche
Engineering MentorHeavy Duty Project Manager at Corning
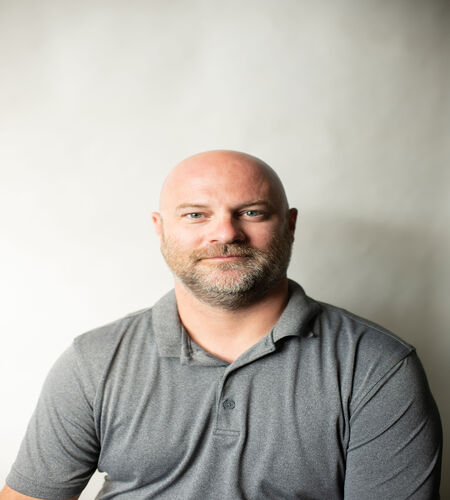
Jeffrey Stott
Engineering MentorEquipment Engineering Manager at Corning
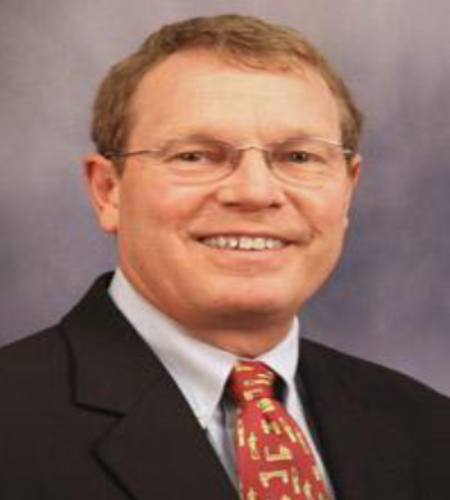
Eric Hellstrom, Ph.D
Academic AdvisorMaterials Science Program Director
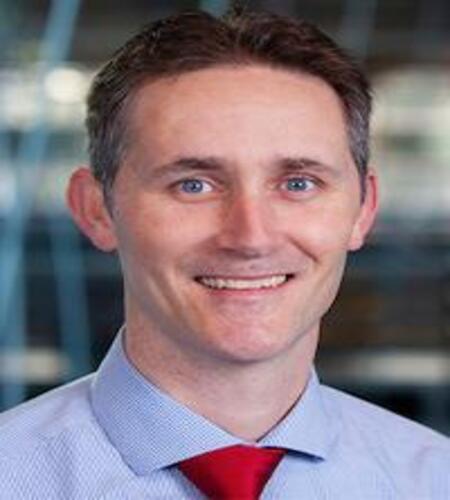
Shayne McConomy, Ph.D
Senior Design ProfessorTeaching Faculty in the Mechanical Engineering Department